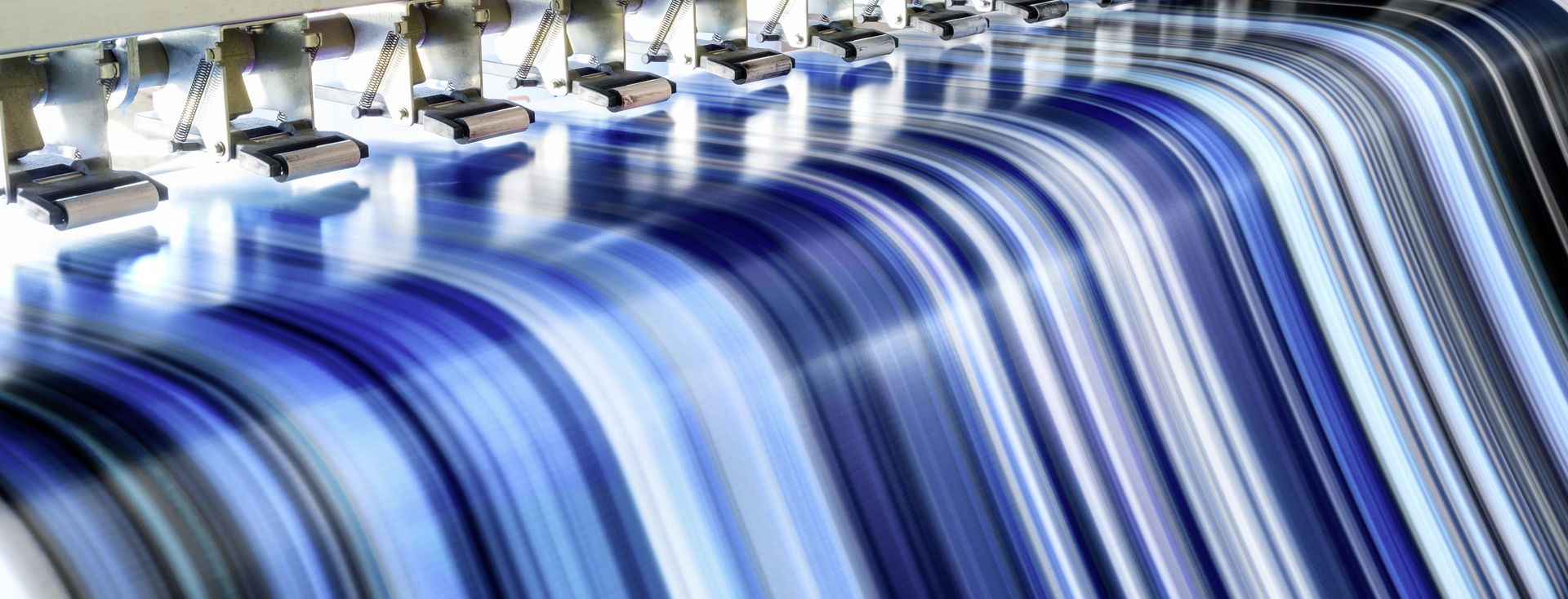
Inkjet printing
Optimization of the ink, the printing process and the substrate with surface science methods
While inkjet technology is declining in the home and office sectors, industrial applications are recording strong growth. Thanks to the multitude of possible combinations of ink types and substrates, as well as low set-up costs, inkjet printing is a very adaptable process. The quality depends very much on the control of the print heads, on the flight behavior of the droplets and on the droplet distribution on the substrate as well as on its wettability. The investigation of the static and dynamic surface tension of the ink as well as the surface properties of the substrate are typical applications for our measuring instruments.
Common applications of inkjet printing
- Packaging printing and individual branding
- Printing on ceramics, decor and glass
- Floor coverings
- Textile printing
- Printable circuits
- 3D printing
Controlling the ink’s wetting behavior with static and dynamic surface tension
Drop formation and spreading is largely controlled by the surface tension of the ink, which is commonly lowered with surfactants. Our tensiometers help to adjust the surfactant concentration by measuring the static surface tension. The critical micelle formation concentration (CMC) as an indicator for the surfactant’s efficiency is measured automatically using a wide concentration range.
To optimize ink in terms of wetting means to regulate the speed with which the surfactant lowers the surface tension. During ink ejection, the surface tension needs to be large enough to ensure meniscus recovery inside the nozzle, and thereby, guarantee a proper drop formation. However, after a very short flight time, the surface tension needs to be low enough to assure proper wetting of the substrate. Our bubble pressure tensiometers monitor the dynamic behavior of the surface tension in a wide range of speed.
Evaluating the wettability of the print carrier and the effect of surface treatment
The surface energy of the substrate defines the wettability and partly controls the adhesion between ink and substrates such as paper or plastics. Our contact angle instruments determine the surface free energy and its division into polar and disperse parts. This energy profile serves to optimize surface preparation steps like plasma or corona treatment.
As ink-jet printing drops of approximately 100 pL are ejected onto a substrate, our picoliter dosing unit, microscope optics, and high speed camera characterize this wetting process very closely to true environmental conditions.
Avoiding foam with the help of foam analysis measurements
Wherever there are surfactants involved in dynamic processes, foam formation can become a challenge to solve. Our instruments for foam analysis offer highly reproducible methods for measuring foam formation in the short-term range of unstable foams. This makes them powerful tools for optimizing antifoam agents added to the ink.