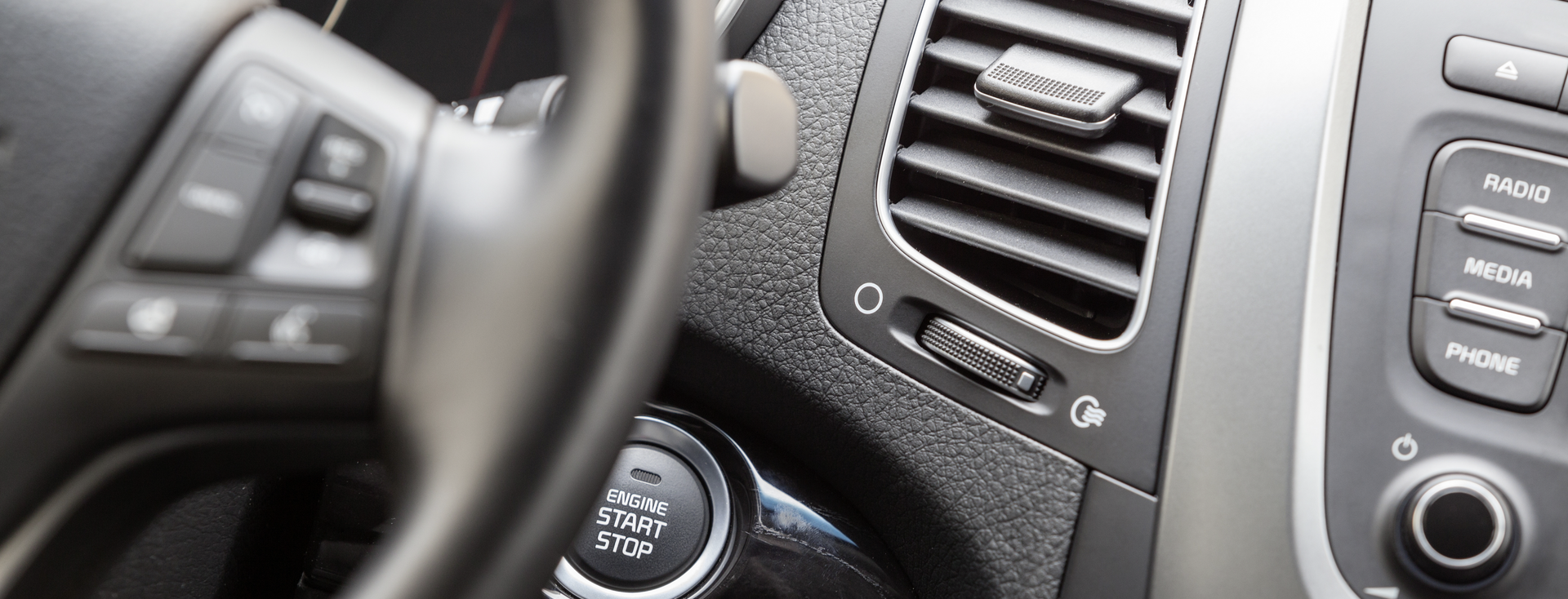
Optimizing flame treatment of polymer surfaces
Mobile contact angle measurements on glass fiber reinforced composite materials for automobile interiors
Polymer-based composite materials are increasingly being used in automobile construction to reduce weight. As a rule, it is necessary to treat the surface of these materials to achieve stable adhesion and coating. Using body trim parts for the automobile interior as an example, we show how flame treatment can be accurately followed using mobile contact angle measurements.
One of our customers observed an unacceptably high reject rate after applying a decorative film – the film became increasingly detached at certain points. Test inks showed no local differences. Within a few hours, various parameters of the flame treatment process on site were varied and the surface free energy was determined at different points. The SFE was calculated based on contact angle measurements at the treated surface with the help of the Mobile Surface Analyzer – MSA. This showed that one side of the workpieces was systematically underactivated, which was presumably due to an increased distance between flame and composite surface.
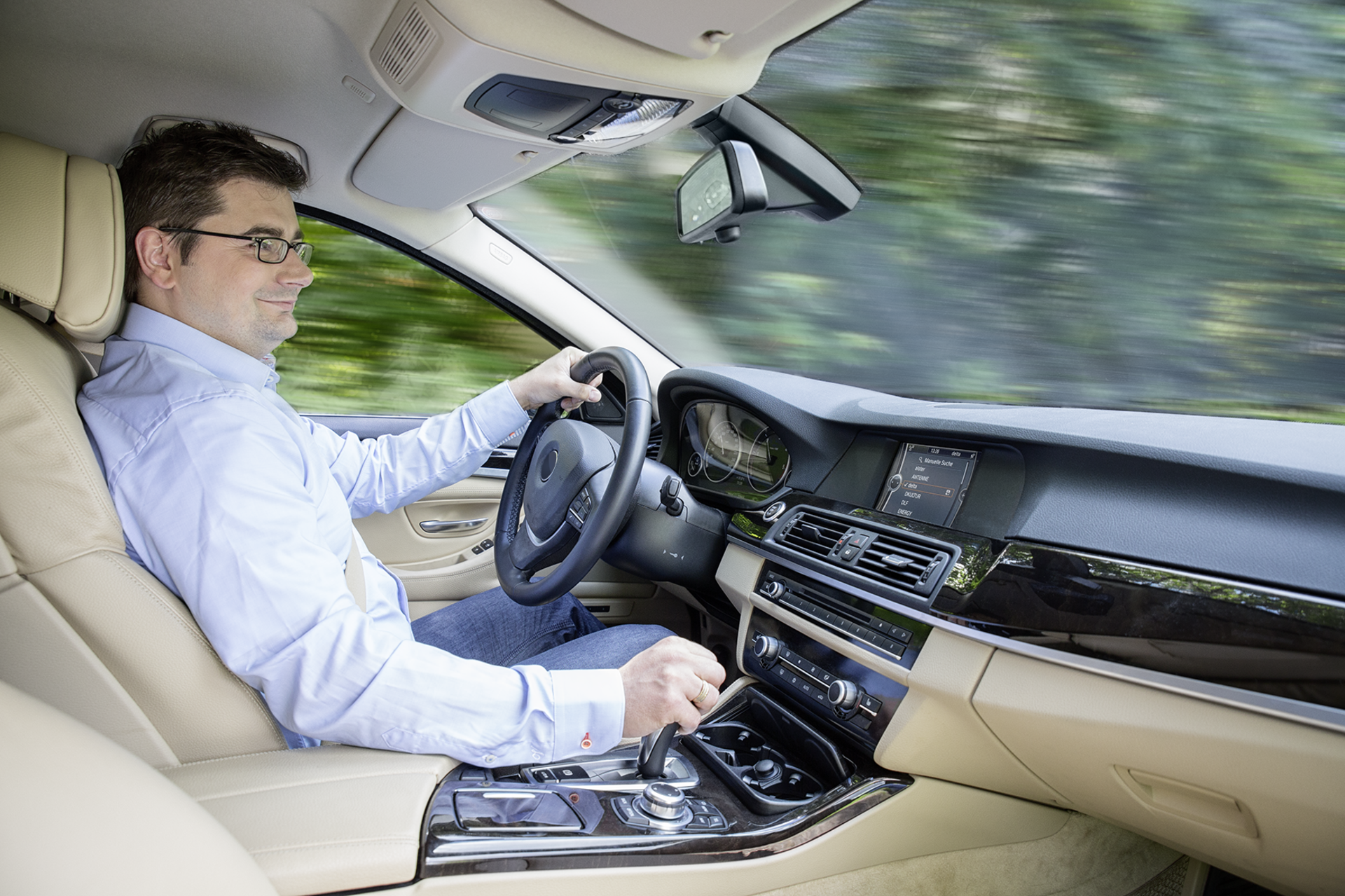
Background
Polymer and composite materials in the automobile industry
New composite materials based on polymers are increasingly being used in the automobile sector as an alternative to materials such as steel, aluminum and glass. The main reason for this is a drastic reduction in weight and consequently an accompanying reduction in fuel consumption and CO2 emissions. In order to satisfy the high quality and safety standards in the automobile industry, such materials must be reliably coated and stably bonded. But this is exactly where problems such as unstable adhesive bonds or detachment of paints and films arise in practice.
Surface free energy and its contribution to adhesion behavior
The reason for such problems is the typically low surface free energy (SFE) of polymers, which impedes the spreading of liquid coatings and a physical-chemical bond between solid and liquid. The surface of polymer materials must therefore first be modified, thus increasing the SFE. In this way, physical effects which determine the adhesion behavior of coatings and adhesives (e.g. spreading coefficient, work of adhesion, interfacial tension) are optimized. Available techniques for modifying polymer surfaces include flame treatment, plasma, corona or chemical treatment. A change in the SFE after treatment can be quantified by contact angle measurements of at least two liquids using the Owens, Wendt, Rabel and Kaelble (OWRK) model [1].
Flame treatment of glass fiber reinforced polypropylene
A supplier of glass fiber reinforced polypropylene parts (GFR-PP) for automobile interiors contacted us and reported problems with the adhesion of decorative film on dashboard covers. The covers were modified by means of flame treatment before applying the film. According to subsequent determination of the SFE with test inks, the effect of the treatment was apparently satisfactory. However, in fact, the decorative film became detached at certain points in an unacceptable number of the activated parts. It was impossible to detect any differences between these problem areas and other flame-treated areas using test inks.
Contact angle measurement as a valid test method
Our answer to the supplier’s unusable experiments with test inks was to measure the contact angle. While test inks provide no information on polar and disperse fractions of the SFE, contact angle measurements enable these to be differentiated and therefore concrete physical parameters, such as the adhesion energy or the interfacial tension, to be calculated. These can therefore be specifically optimized, thus enabling maximum adhesion between adhesive or coating and surface to be achieved. A comparison of test inks and contact angle measurements is available in the form of an application report [2] and is described in more detail in [3].
Experimental part
Contact angle measurements were carried out on site at the customer’s premises in a production hall using the fully automatic Mobile Surface Analyzer – MSA. The measurements were non-destructive. With the MSA, it is not necessary to cut up the large, non-flat parts or to transfer the samples to a test laboratory. During the measurement, two test liquids (water as the polar and diiodomethane as the non-polar, disperse liquid) were deposited on the surface of the composite part and the drop shape was subsequently analyzed. Measurements on the untreated and flame-treated PP are shown in Fig. 2 by way of example.
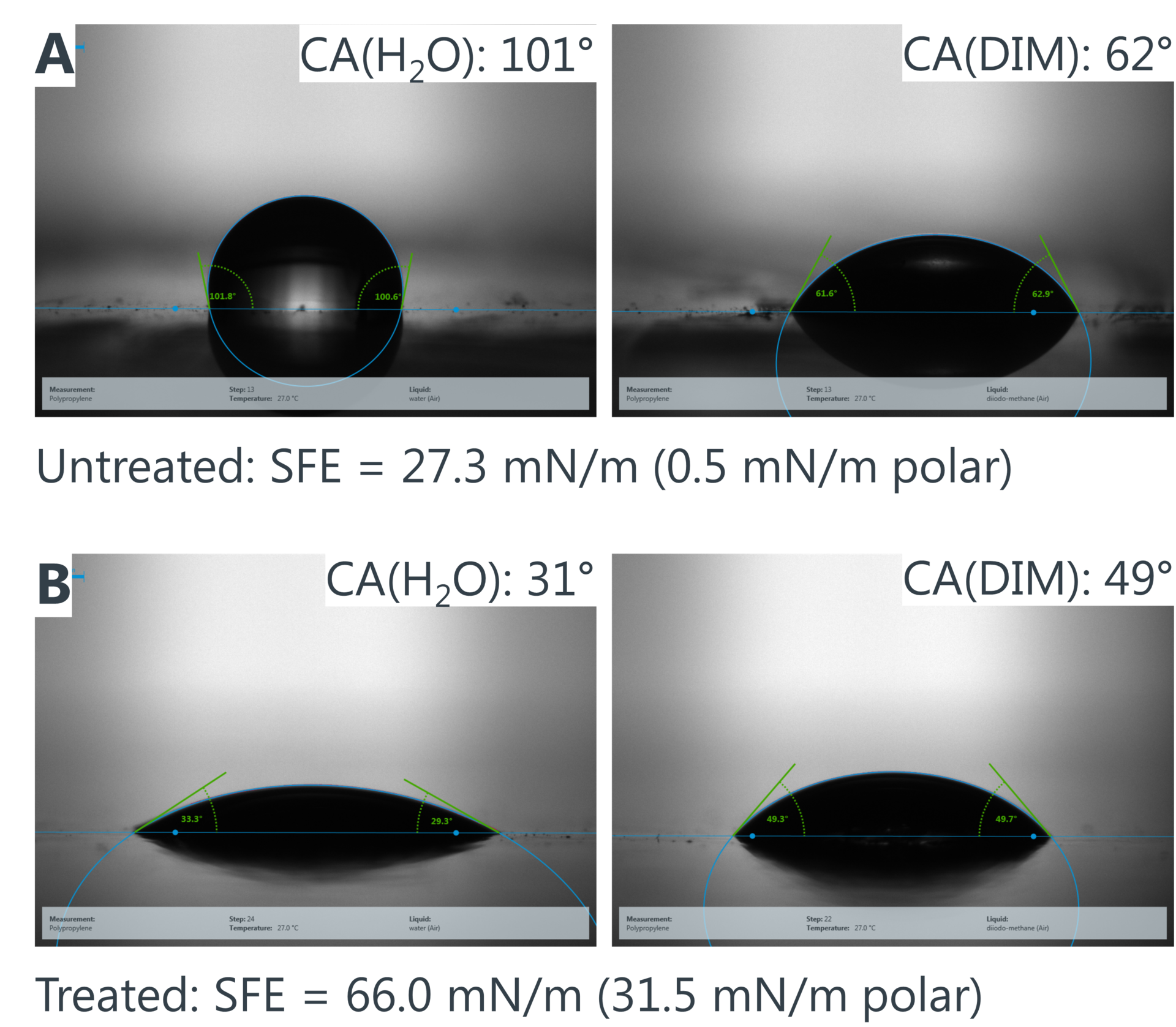
The SFE values were calculated in accordance with OWRK using the parameters listed in Table 1.
Test liquid | σ [mN/m] | σd [mN/m] | σp [mN/m] |
Water | 72.8 | 21.8 | 51.0 |
Diiodomethane | 50.8 | 50.8 | 0.0 |
Tab. 1: Surface tension (σ) with polar (p) and disperse (d) fractions of the test liquids used.
Screening of the flame-treatment parameters was carried out based on contact angle measurements. For this purpose, three dashboard covers were in each case treated with the same parameters (gas flow, gas/air ratio, etc.). The SFE with polar and disperse fractions was then determined at eight different spots on each sample (Fig. 3) and the next three samples were then flame-treated and measured under different conditions. In total, 24 parts were flame-treated under eight different conditions and more than 380 contact angle measurements were carried out with the mobile instrument and subsequently evaluated on site in only about two hours.
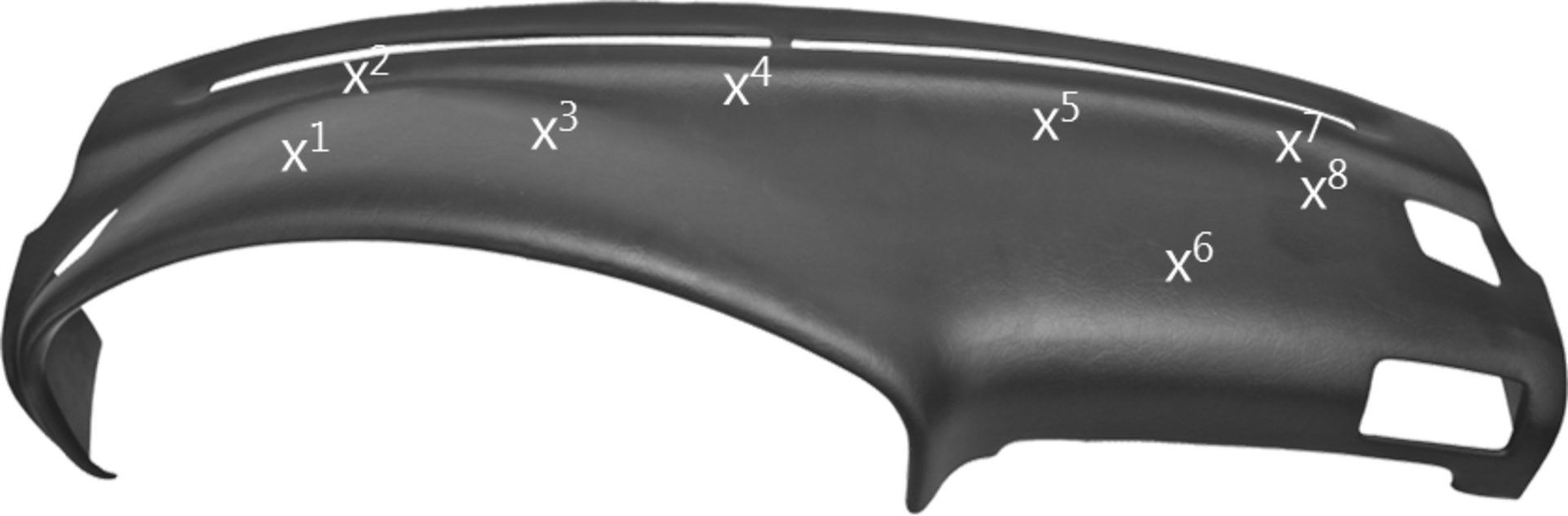
Results
The SFE values with polar and disperse fractions determined on the basis of the contact angle measurements for all eight areas investigated are shown by way of example in Fig. 4 for sample 11.
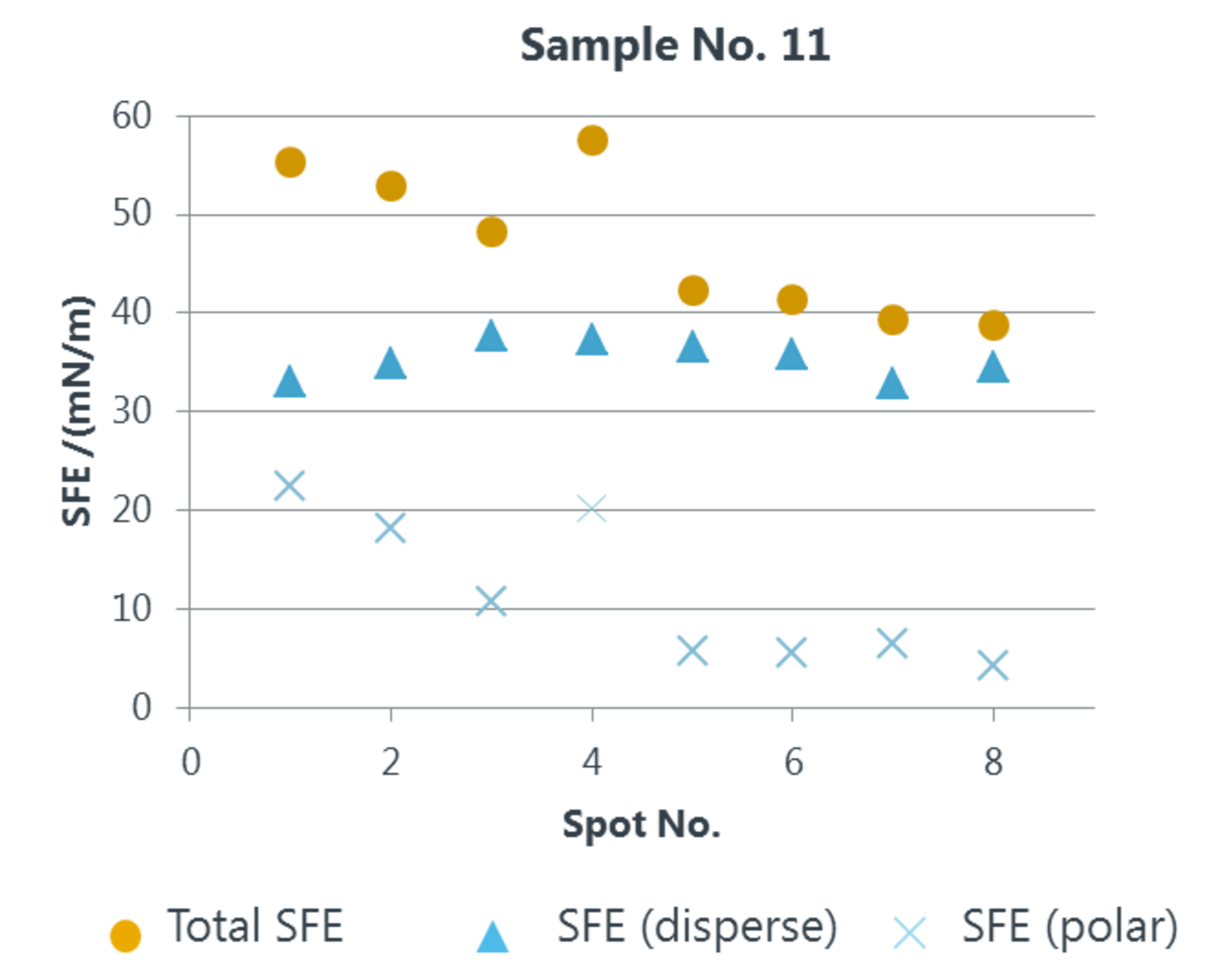
While the regions 1-4 have comparably high SFE values and at the same time, in particular, high polar fractions due to the flame treatment, the values for the regions 5-8 are considerably lower. Accordingly, the left-hand side of the sample is well activated and provides adequate interaction for a stable bond in a subsequent coating process. On the other hand, the right-hand side with the spots 5-8 exhibits only a small change in SFE values compared with an untreated surface (cf. Fig. 2).
A glance at the complete overview of the calculated SFE values for all samples and measuring regions substantiates this finding (Fig. 5). One side of the flame-treated parts (spots 5-8) was evidently systematically underactivated.
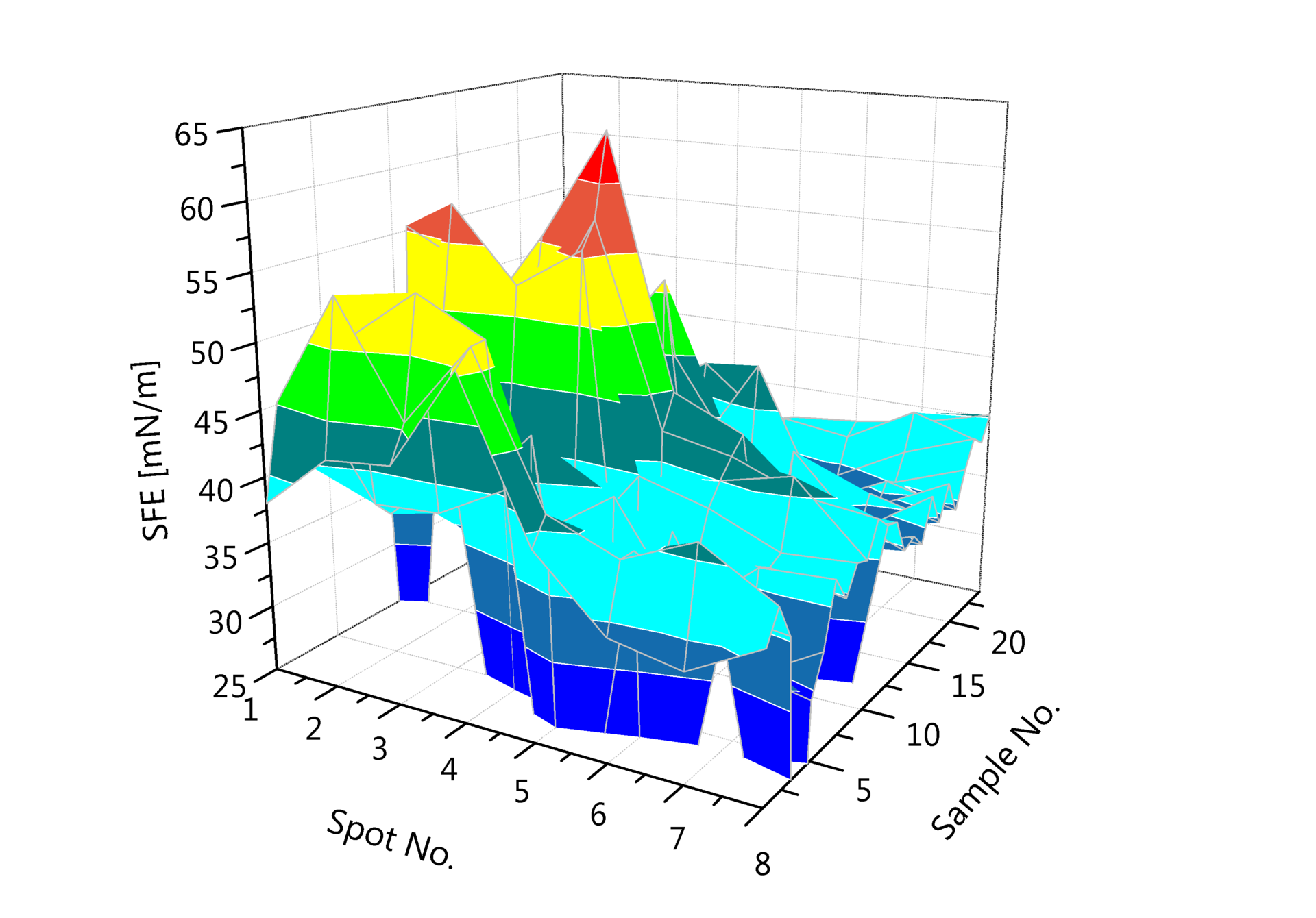
This finding provides a good explanation for the customer’s observation that a subsequently applied decorative film exhibited adhesion problems, particularly in this area. One solution for the inadequate modification of the right-hand side of the sample is to adjust the distance between flame and sample in this area.
Furthermore, an optimum for the modified flame-treatment parameters can be quickly found by looking at the SFE values of the differently treated parts. In each case, three samples were flame treated under the same conditions. Samples No. 10 to 12 exhibit the greatest increase in SFE, in particular the polar fractions, as a result of which the parameters used here signify the optimum conditions for treatment with good subsequent adhesion.
Summary
The treatment of polymer composite materials is indispensable for stable coating. However, while test inks or measurements with only one test liquid are unable to provide information on the polarity of the surface and results are highly user-dependent, mobile measurements of the surface free energy with the MSA offer a reliable, quantitative measurement of the surface modification. This was demonstrated by way of example with the flame treatment of dashboard covers made from glass fiber reinforced polypropylene. Mobile contact angle measurements showed an unequal activation along the surface. Screening of eight different flame-treatment settings enabled the parameters to be quickly optimized. A two-hour, non-destructive measurement directly on site enabled the rejection rate to be reduced quickly and efficiently.
Bibliography
- [1] D. K. Owens, R. C. Wendt, “Estimation of the Surface Free Energy of Polymers”, J Appl Polym Sci 13, 1741 (1969).
- [2] T. Willers, M. Jin, AR 272 - “Why test inks cannot tell the full truth about surface free energy” (2014).
- [3] K. L. Mittal, “Advances in contact angle, wettability and adhesion”, Vol. 2, Wiley-Scrivener, ISBN 978-1119116981 (2015).