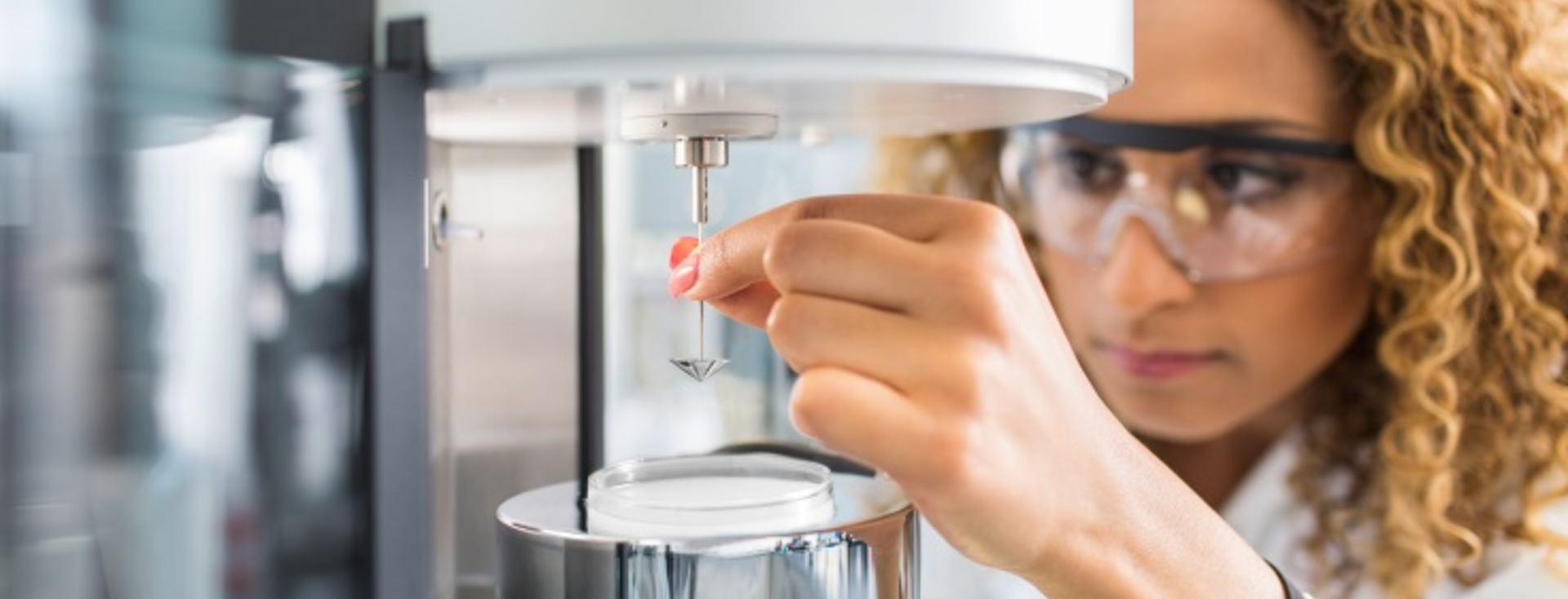
Characterizing particle size of filler materials quickly and easily
Sedimentation measurements on calcium carbonate powders with a tensiometer
Finely dispersed, inorganic filler materials are frequently used to optimize the mechanical and physical properties of materials. As well as the wetting behavior of such particles, which can be investigated by means of Washburn measurements, their size distribution also plays an important role in the quality of the end product. In the case described here, using Washburn measurements, one of our customers was unable to establish small differences between various calcium carbonate samples, which may have explained the different behavior of the powders in the production process. In our application lab, we carried out sedimentation measurements on various batches of these powders in isopropanol and observed differences in their sedimentation behavior.
Based on a simple model, we have been able to draw conclusions from the measured graphs relating to the particle size distribution in the samples, and, at the same time, differentiate particularly between monodisperse and polydisperse samples. Accordingly, a sedimentary measurement enables the particle morphology to be investigated quickly and easily and can be carried out in addition to wetting analysis with one and the same measuring instrument, our Force Tensiometer – K100.
Background
Quality control of filler materials
Inorganic particles, ranging in size from nanometers to microns, are used as filler materials in polymers and functional materials for building construction, paper manufacturing and in adhesives and paints. They help to improve and control mechanical and rheological properties of the product and to reduce material costs.
With regard to the dispersion of the filler materials and the resulting product quality, two characteristics of the powder in particular must be highlighted: firstly, their wettability by the bulk matrix and, secondly, the size and morphology of the particles. Loss of quality due to these aspects leads to inhomogeneous distribution of the particles and, as a consequence, to negative product properties, e.g. reduced impact resistance [1].
The wetting behavior, which is associated with the surface free energy of the filler material particles, can be determined by means of the Washburn method for powder samples. [2] Preliminary investigations on the powder samples discussed here were carried out by our customer using this method. However, as the contact angle measured by the Washburn method depends only on the surface free energy of the powder and not on its porosity, the results for the chemically identical samples were the same, as expected. Consequently, the established different behavior of the powders in the production process must have been due to the particle size.
Experimental methods for exactly investigating the particle structure, e.g. electron microscopy, are often very laborious. In contrast, we show how distinction can be made between different particle samples with only a little effort by measuring the sedimentation behavior. A major advantage is the experiment’s setup, which is very similar to a Washburn measurement. This enables the wetting and sedimentation behavior of powders to be measured independently of one another, but with one and the same measuring instrument.
Sedimentation and particle size
Various forces, which affect sedimentation, act on particles in a suspension. Gravity is counteracted by buoyancy and a friction component. Equilibrium is established between these forces so that particles sink at a constant speed (Stokes’ law) [3]:
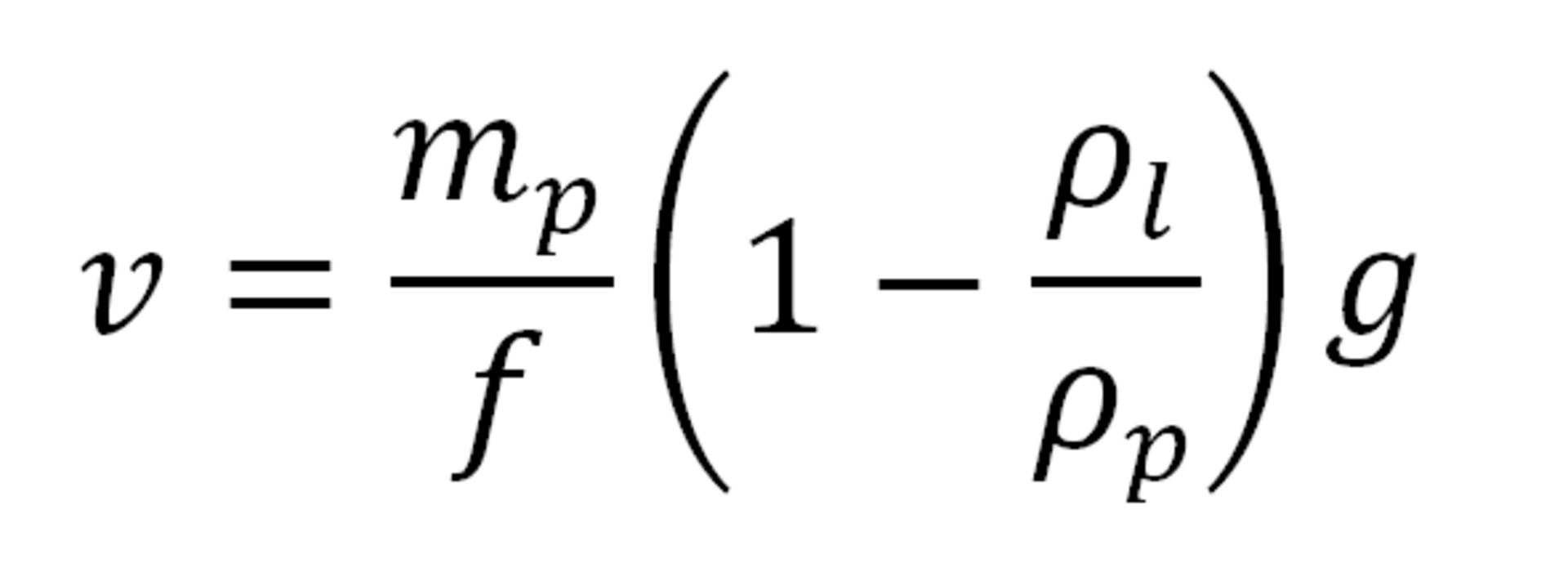
Here, mp is the mass of the settling particles, f is the friction factor which depends on the size and shape of the particles and on the viscosity of the bulk medium, ρl is the density of the bulk liquid, ρp is the effective density of the particles, and g is the acceleration due to gravity.
The sedimentation rate differs for particles of different density, size and shape and, assuming a constant concentration, is proportional to the detected increase in mass over time:
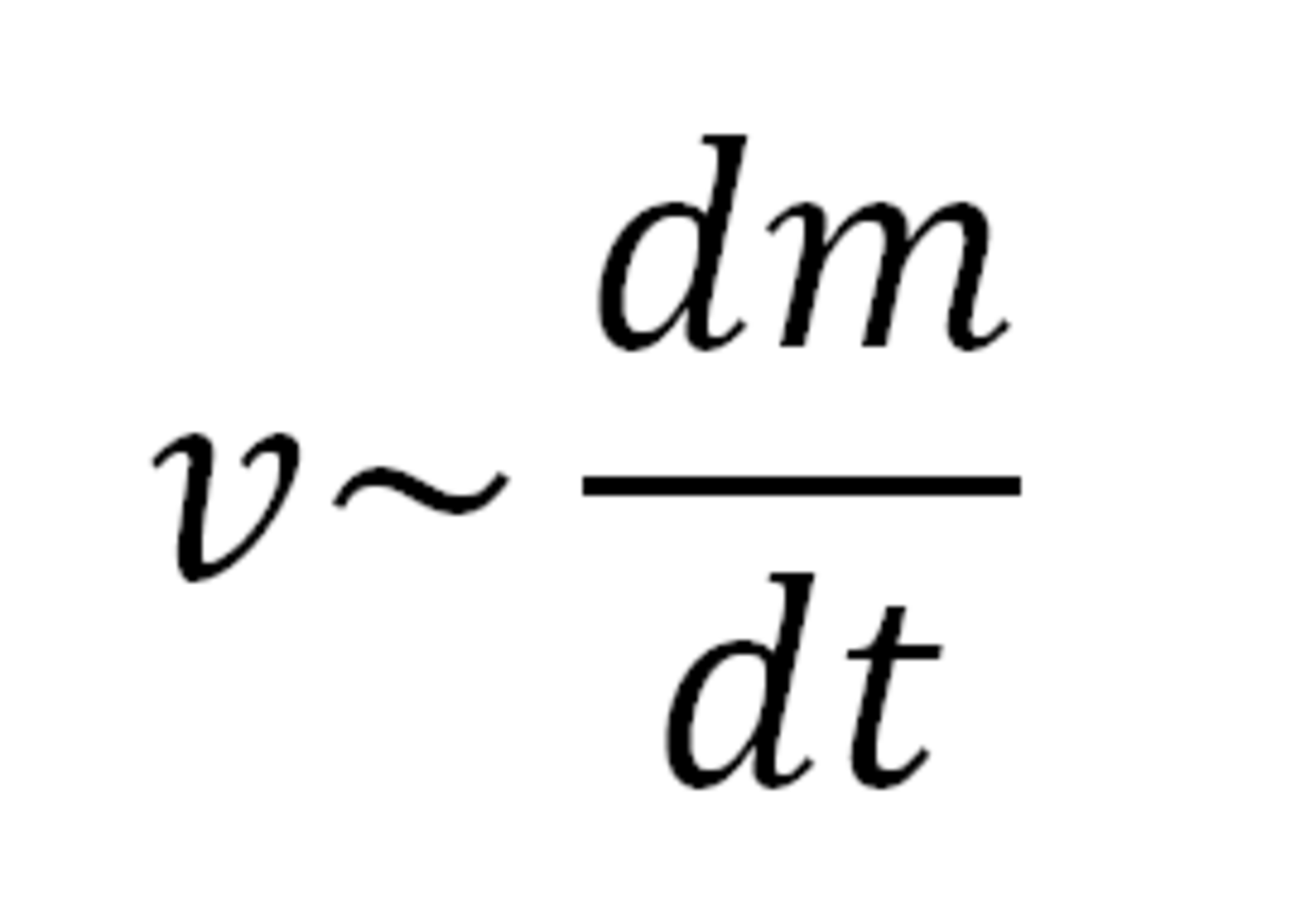
Normalizing with respect to the gravitational constant results in the sedimentation coefficient S [s or Svedberg = 10‑13 s], which is frequently used in the technical literature to describe the sedimentation behavior [4]:
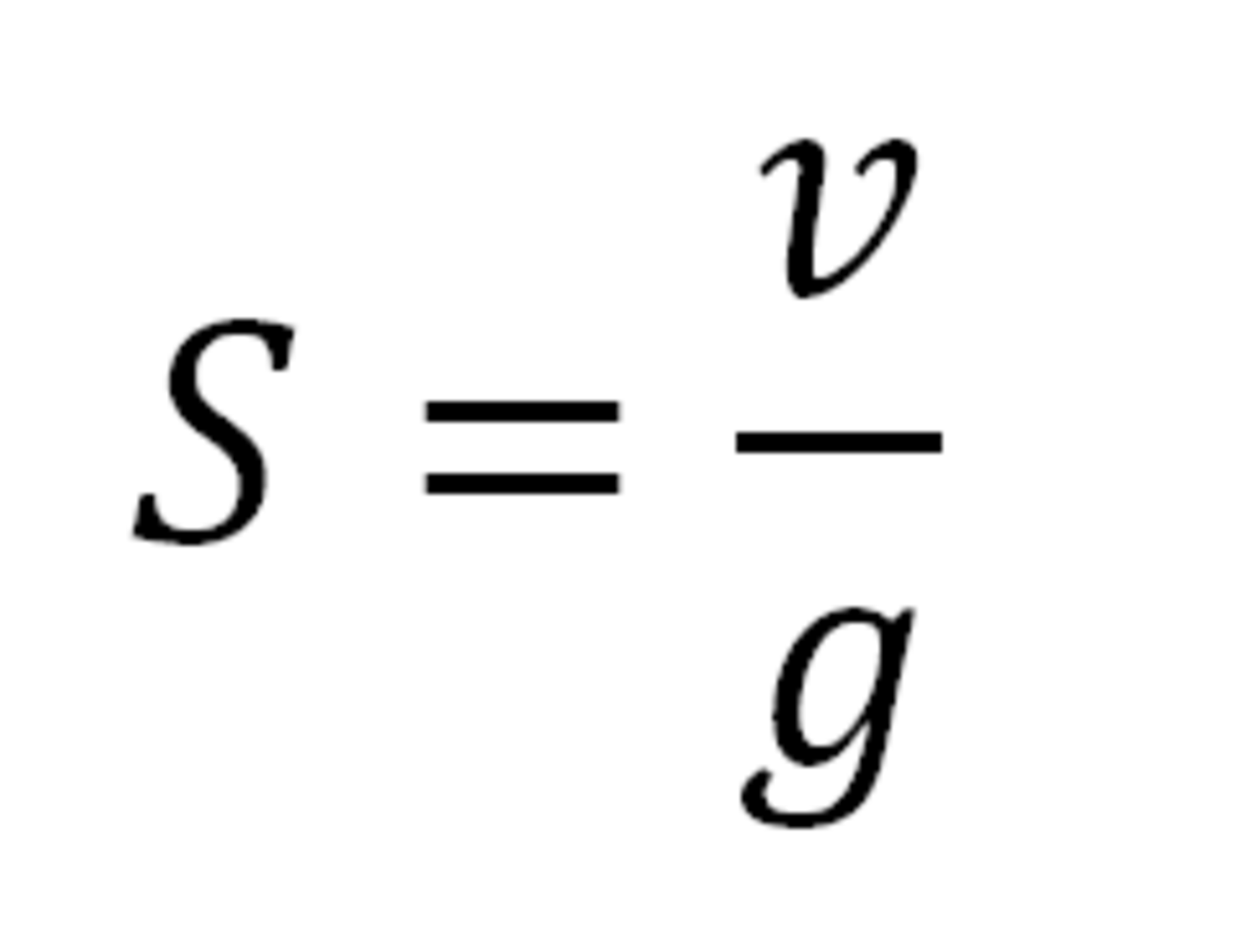
By this means, monodisperse samples, that is to say those with uniform particle shape and size, can easily be differentiated from polydisperse samples. The former have only a constant rate of rise for the increase in mass with respect to time, while the latter can exhibit a wider distribution or several defined rates of rise.
Experimental part
The various calcium carbonate powders (samples 1-3) were investigated. The powders are hydrophobic and are therefore not wetted by water but remain on the surface. Isopropanol was therefore chosen instead as the bulk phase for the sedimentation measurements. A 1% suspension of each powder sample was prepared in isopropanol. All measurements were carried out with our Force Tensiometer – K100 at room temperature. Stirring for several minutes with the help of the integral magnetic stirrer ensured a homogeneous initial distribution of the particles. The measurement was started immediately after stirring. For this purpose, a probe (SH0640) was immersed to a depth of 20 mm in the suspension in a software-controlled way and the increase in mass was recorded over a period of 600 s (Fig. 1).
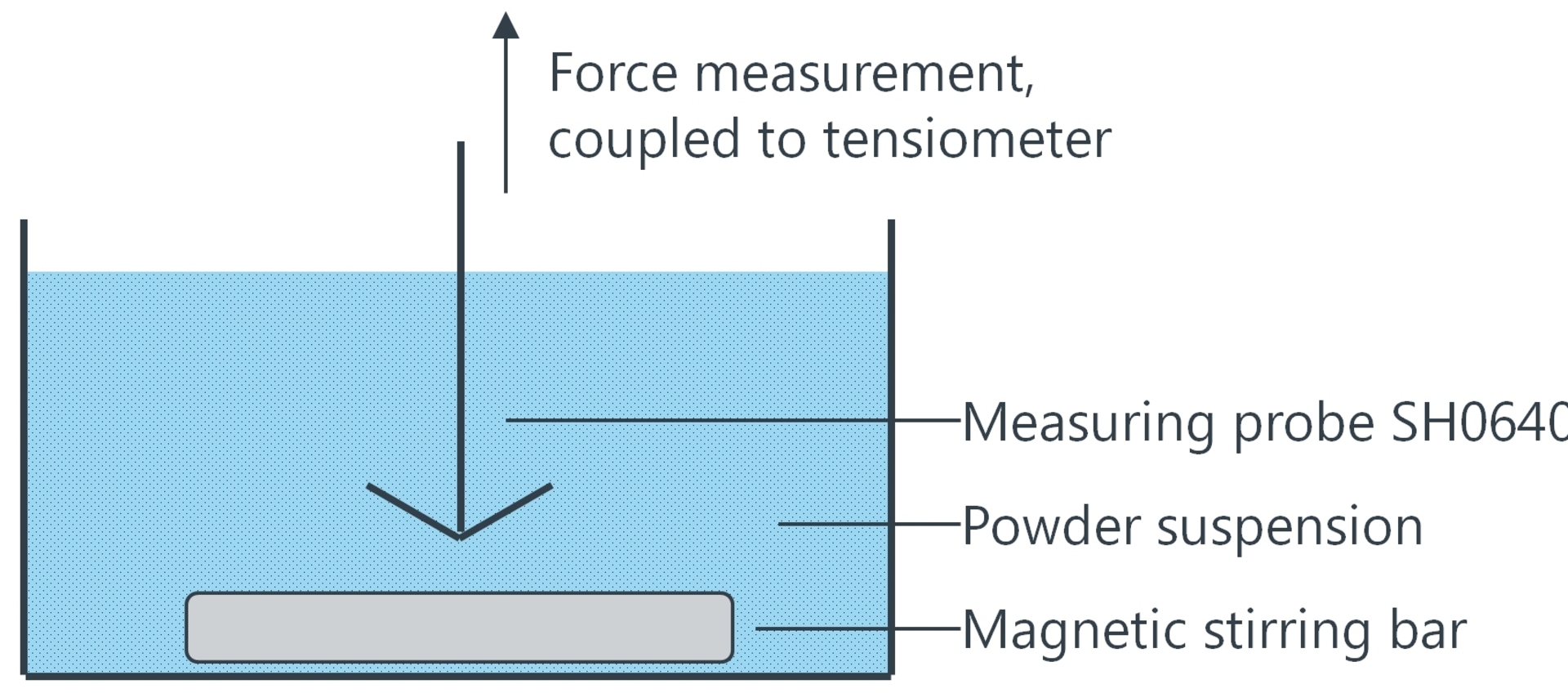
Results
Fig. 2 shows the characteristic of the detected mass against time for two experiments on each sample 1-3. Here, it can be seen that the two graphs for each sample are very similar, i.e. the sedimentation behavior can be measured with good reproducibility.
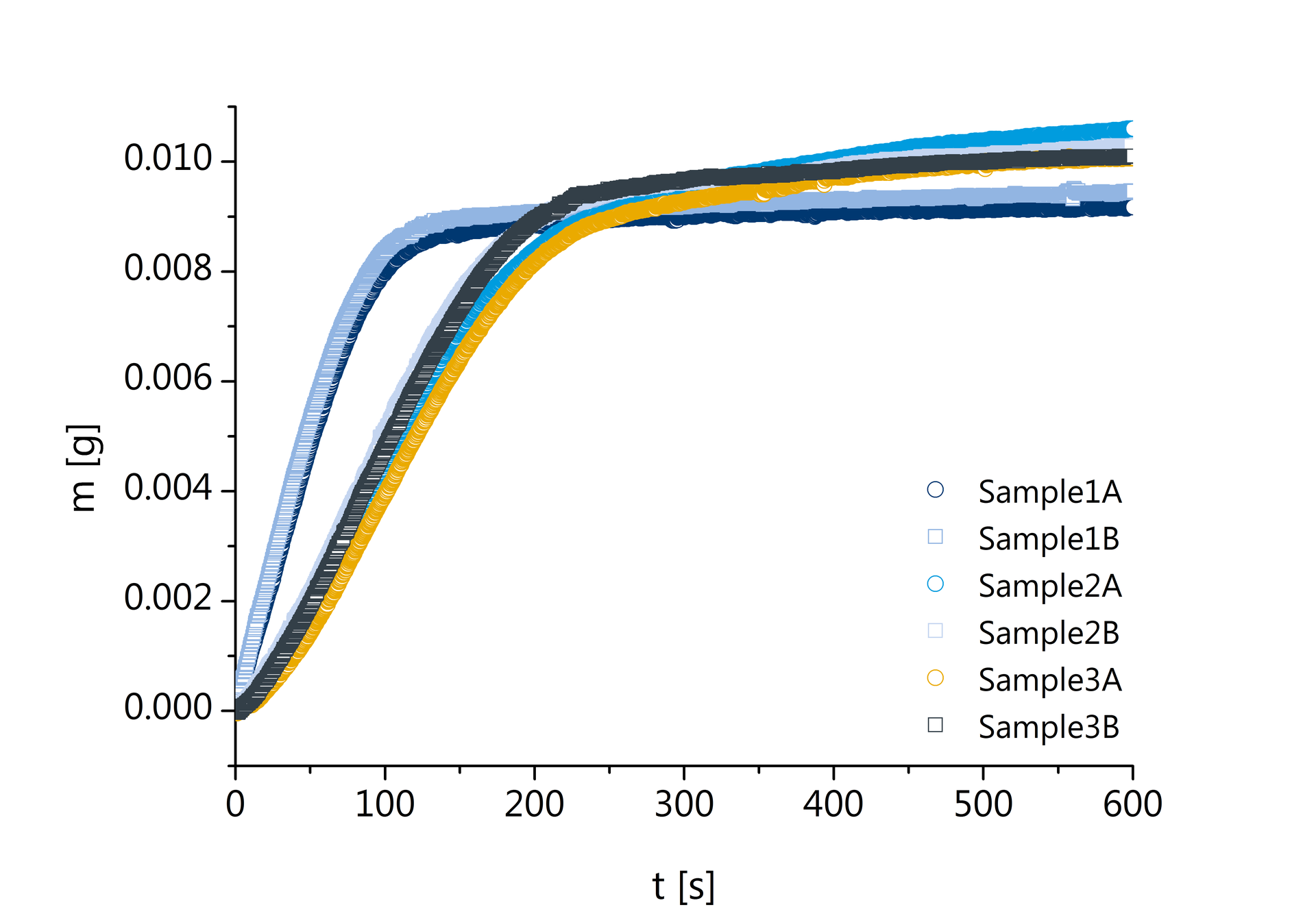
When comparing the three samples with one another, it can be seen that Sample 1 exhibits a considerably faster increase in mass compared with Sample 2 and Sample 3, which is shown by comparable graphs. The total increase in mass after 600 s hardly differs for all three samples and is approximately 10 mg.
The rate of sedimentation dm/dt is plotted in Fig. 3 for one measurement on each of the three samples. Here too, a difference can be clearly seen between Sample 1 and the other two samples. For Sample 1, there is a constant sedimentation rate over the first approximately 45 s of about 100 µg/s before this rapidly reduces to a value of 0 and the sedimentation is complete. Accordingly, the particles in this sample are rather monodisperse particles with a close size distribution which sink at the same, constant rate.
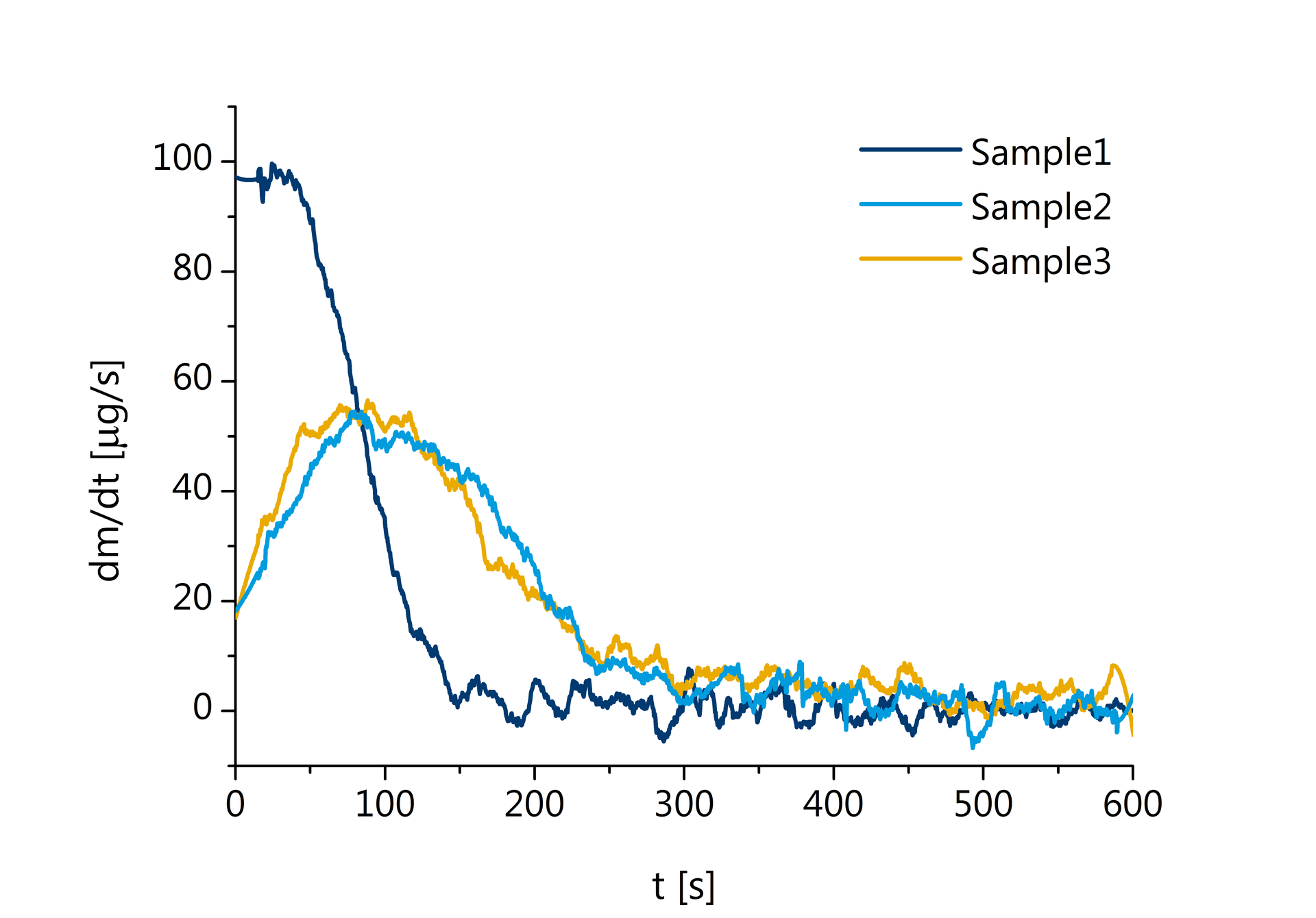
Samples 2 and 3 have a different characteristic. Here, a wide distribution of sedimentation rates between 10 and 60 µg/s can be seen over the first approximately 250 s, which points to a polydisperse particle distribution with different densities, sizes and possibly also the formation of agglomerates. With regard to a required homogeneous distribution of the filler material particles in the matrix of the finished product, the use of particle sample 1 is therefore recommended, wherein it must be ensured that the curing of the product occurs sufficiently quickly in comparison with the sedimentation of the particles.
Summary
Inorganic micro and nanoparticles are an important ingredient of paints, adhesives, papers and construction materials. Their quality as a filler material is strongly dependent on the size distribution of such particles. Using calcium carbonate powders as an example and with the help of sedimentation measurements using the Force Tensiometer – K100, we show how, with little experimental effort, differentiation can be made between monodisperse particles with close size distribution and polydisperse particles. For our customer, these measurements were a helpful addition to the Washburn measurements which he had already carried out himself. In combination with the Washburn method for investigating the wetting behavior of such particles, the K100 therefore offers extensive characterization possibilities.
Bibliography
- [1] W.C.J. Zuiderduin, C. Westzaan, J. Huétink, R.J. Gaymans, Polymer 2003, 44, 261.
- [2] C. Rulison, Krüss Application report AR224, 2001.
- [3] J.C. Berg, An Introduction to Interfaces and Colloids, World Scientific Publishing, Singapore, 2010, p. 387 ff.
- [4] J. Lebowitz, M. S. Lewis, P. Schuck, Protein Science 2002, 11, 2067.
As mentioned in this application report, a K100 Force Tensiometer had been used for carrying out the measurements. The same measuring methods, only with improved precision and ease of use, can now be performed with the up-to-date Tensíío instrument.