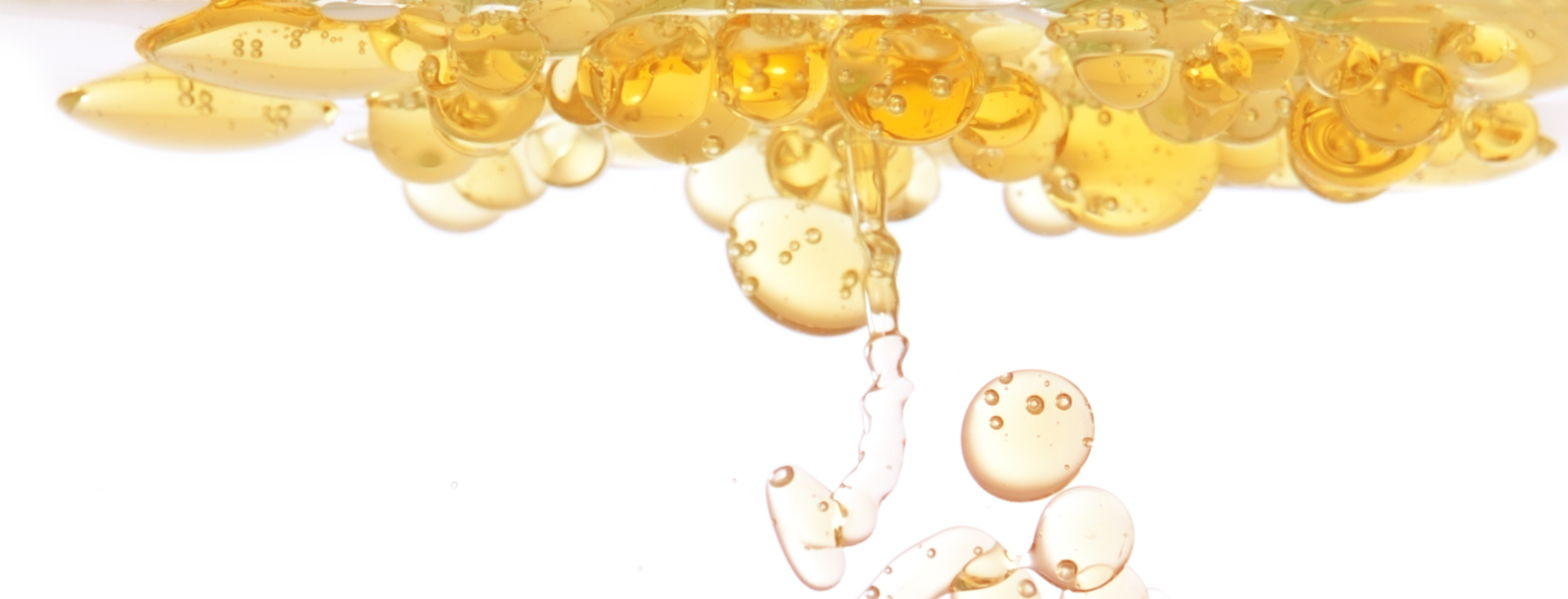
Interfacial Rheology of Particle-Laden Interfaces
Formation and stability of Pickering emulsions
A guest article from the University of Calgary in Alberta (Canada)
Interfacial tension measurements are conventionally conducted to quantify the adsorption of surfactants and particles at liquid-fluid interfaces. Although these tests provide valuable information regarding the formation of emulsions, they do not reveal the structure of the generated particle-surfactant interfacial layer representing the stability of emulsions. We study the influence of cellulose nanocrystals (CNC) as a green and biocompatible source of nanoparticle dispersion on the oil-water interfacial viscoelasticity and consequently on the emulsion formation and stability. By comparing the viscoelasticity data with confocal and cryogenic scanning electron microscopic images of the oil-water interface, we found the high viscoelasticity modulus corresponds to interconnected structures of surface-activated CNC particles at the interface. Interfacial rheology measurements are conducted in oil-water systems where both fluids have low viscosity to minimize the effect of bulk viscous forces. Due to the wide applications of high viscosity oils in food, pharmaceutical, and oil industries, we develop an emulsification map and extend our findings to high viscosity oils, where the knowledge of interfacial viscoelasticity is required.
Background
Cellulose nanocrystals (CNCs) are natural-based, rod-shaped, and highly crystalline colloidal particles extracted from wood, cotton, or other plant sources. CNCs have received lots of attention as emulsion stabilization agents. In CNC-stabilized emulsions, the adsorption of CNCs to the interface, their surface charge, and their considerably large size prevent the coalescence of droplets, resulting in high stability of the thus formed Pickering emulsions. The effect of electrostatic forces and steric repulsion on the CNC-stabilized emulsions have been extensively studied in the literature [1, 2]. However, the mechanical properties of CNCs at liquid-liquid interfaces have received less attention.
Interfacial viscoelasticity, representing the mechanical properties of the interface, may significantly influence the properties of liquid-liquid interfaces. The response of mobile interfaces under specific deformations is employed to characterize the strength of the interfacial film [3, 4].
Dilatational interfacial rheology sheds light on two interfacial properties, i.e., elasticity and viscosity, resulting from the change in the surface area. These properties have a different influence on emulsion formation and stability. The dependency of the interfacial tension (IFT) on the degree and speed of change in surface area are called surface elasticity and viscosity, respectively. Elastic (storage) and viscous (loss) modulus are obtained by changing the interface area sinusoidally and measuring the resulting IFT over time. The response of the interface is expressed in terms of summation of viscous and elastic contributions as

where E is called the “surface dilatation modulus”. The measured E has two parts: real (E') and imaginary (E''), reflecting the elasticity and viscosity, respectively. In this study, the interfacial viscoelasticity modulus of CNC-laden interfaces is measured using drop oscillation method (ODM) with a KRÜSS DSA 100. [5]
Experimental section
Material and sample preparation
A 3 wt.% CNC dispersion (Alberta Innovate) is used as the source of nanoparticle dispersion. CNC nanoparticles in the suspension are rod-shaped and crystalline with 100‑500 nm in length and 5-15 nm in diameter. Hexadecyl trimethylammonium bromide (CTAB, Sigma) with the critical micelle concentration (CMC) of 0.92 mmol/L is used as the cationic surfactant. The oleic phases are heptane (anhydrous, 99%, Sigma:
ρ = 0.684 g/cm3, η = 0.376 mPa s) and a viscous mineral oil sample
(Drakeol 35: ρ = 0.876 g/cm3, η = 135 mPa s). CNC-CTAB dispersions are prepared at different concentrations and are used for emulsion preparation and interfacial tension/rheology measurement.
IFT and rheology measurements
The IFT of CNC-CTAB dispersions with oleic phases is measured using the pendant drop method (DSA100, KRÜSS). A pendant drop of the aqueous phase is formed at a stainless steel needle (outer diameter=1.8 mm) immersed in 40 mL oil sample. We record the data from the sample for 8000 seconds. The elasticity of the interface is measured by imposing a sinusoidal perturbation in the surface area of the drop and analyzing the IFT response using the Fourier transform. The drop is oscillated with the frequency of 1 Hz and the amplitude of 5% of the drop surface area, found through a previous systematic study, to ensure the linearity of the response. Measurements are conducted with dye in oil and aqueous phases, as these samples are used later in emulsification tests.
Results
Interfacial viscoelasticity
The IFT of pure CNC dispersion remains unchanged upon varying the volume (surface area) of the drop (Fig. 1a). In contrast, the IFT of pure CTAB solution responds to the deformation cycles with the sinusoidal variation (Fig. 1b). For the soluble surfactants such as CTAB and surface modified CNC particles, once the surface area is changed, there is an exchange of surfactants and particles between the bulk to the interface until the equilibrium surface tension is achieved. Thus, in these systems, the surface tension is not constant, and depends on the degree and speed of change in area and the rate of the surfactant adsorption/desorption to and from the interface. The magnitude of IFT variations in the CNC-CTAB dispersion (~ 1 mN / m) is significantly increased compared to the pure CTAB solution (~ 0,5 mN / m); see Fig. 1c. Surfactants (CTAB molecules) are smaller compared with surface modified CNC particles. Thus, they may have a higher adsorption-desorption rate and respond faster to the area variations. Fig. 1d shows the interfacial elasticity (left axis in red) and viscosity (right axis in blue) over a range of CNC concentrations at CTAB concentrations of 0.05 (circle symbols), 0.10 (triangle symbols), and 0.50 (square symbols) CMC. In all tested concentrations, the magnitude of interfacial viscosity is significantly less than the elasticity. The magnitude of interface elasticity enhancement depends on both CNC and CTAB concentrations. Fig. 1d indicates a threshold of CNC concentration (0.5 wt.%) at which the elastic modulus of the CNC-CTAB system significantly increases. The increased viscoelasticity in the presence of CNC-CTAB particles compared with the viscoelasticity of the surfactant solution might be due to the larger size of adsorbed CNC-CTAB particles at the interface.
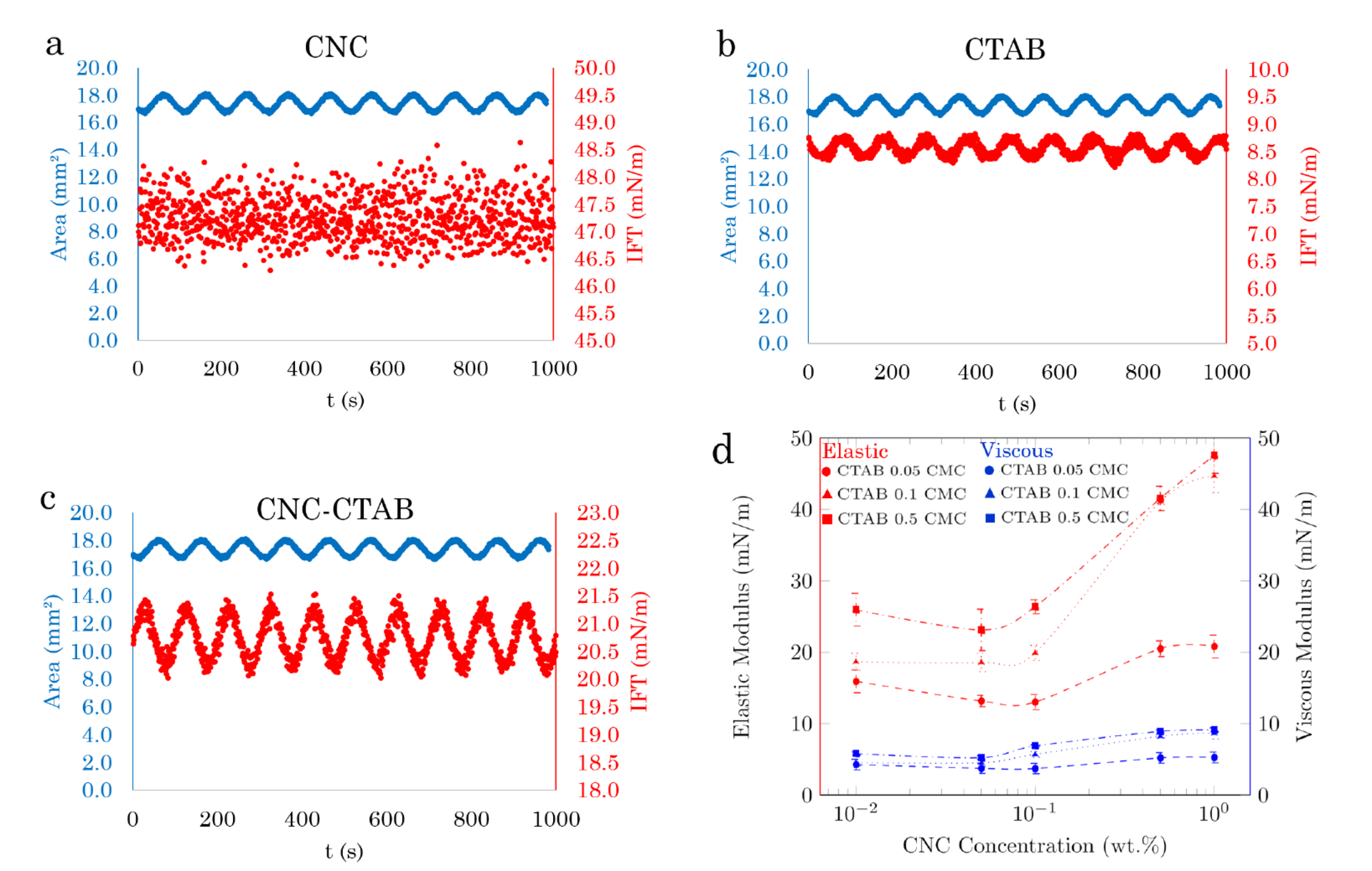
Emulsion formation
Emulsions are prepared from same volume of oil and aqueous phases with either shaking or magnetic stirring. Oil in water (O/W) emulsions are generated and their stability depends on the CNC-CTAB concentration. DI-water and CNC dispersions do not form emulsions by low input energy techniques due to the high IFT (46 - 50 mN / m) of these systems. CTAB solutions emulsify oil, but the emulsion is only stable for about 20 minutes. The minimum CNC and CTAB concentrations to generate stable emulsions are 0.50 wt.% and 0.10 CMC, respectively. Fig. 2 presents the emulsion formation and stable/unstable emulsion zones on the plane of CNC-CTAB concentrations. The generated emulsions from four dispersions of (CNC, CTAB) at (0.5 wt.%, 0.1 CMC), (1 wt.%, 0.1 CMC), (0.5 wt.%, 0.5 CMC), and (1wt.%, 0.5 CMC) remain stable for more than 6 months. These four dispersions have high interfacial elastic moduli (in the range of ~ 40 - 50 mN / m) compared with other CNC-CTAB dispersions (Fig. 1d).
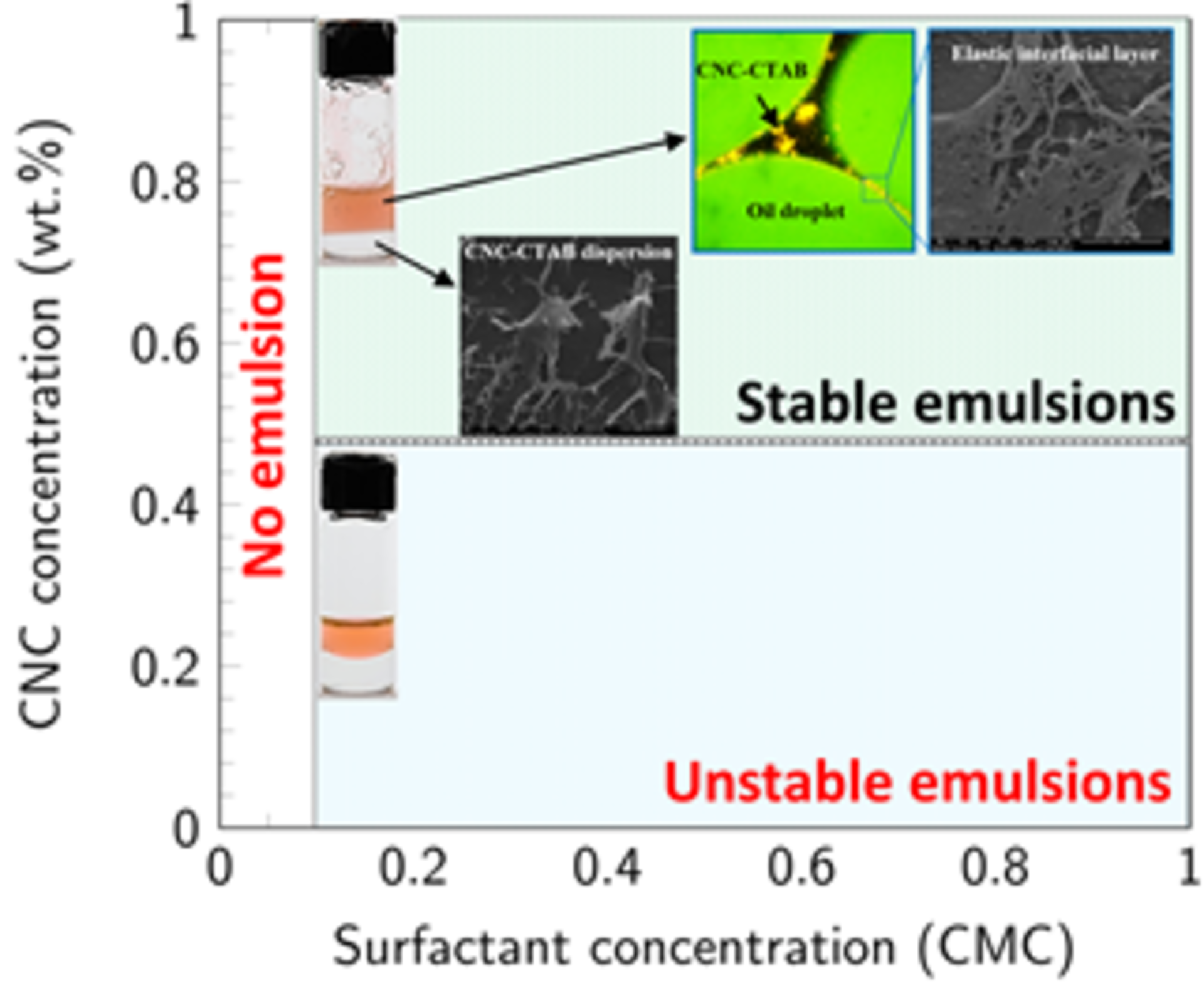
Medium internal phase emulsion
The medium internal phase emulsions (MIPE) are generated by adding consecutive volumes of oil to the initially stabilized emulsions. Fig. 3 shows confocal micrographs of emulsions prepared at (CNC 1.00 wt.% + CTAB 0.10 CMC) with Voil/VWater of 1, 2, 3, and 4. The oil phase and CNC particles are shown in green and orange, respectively. Confocal images show the presence of CNC particles at the surface of oil drops.
The average drop size increases as Voil/VWater increases from 1 to 4. As the oil volume increases, the coverage of CNC-CTAB particles at the interface decreases, hence, emulsions with larger oil drops are formed.
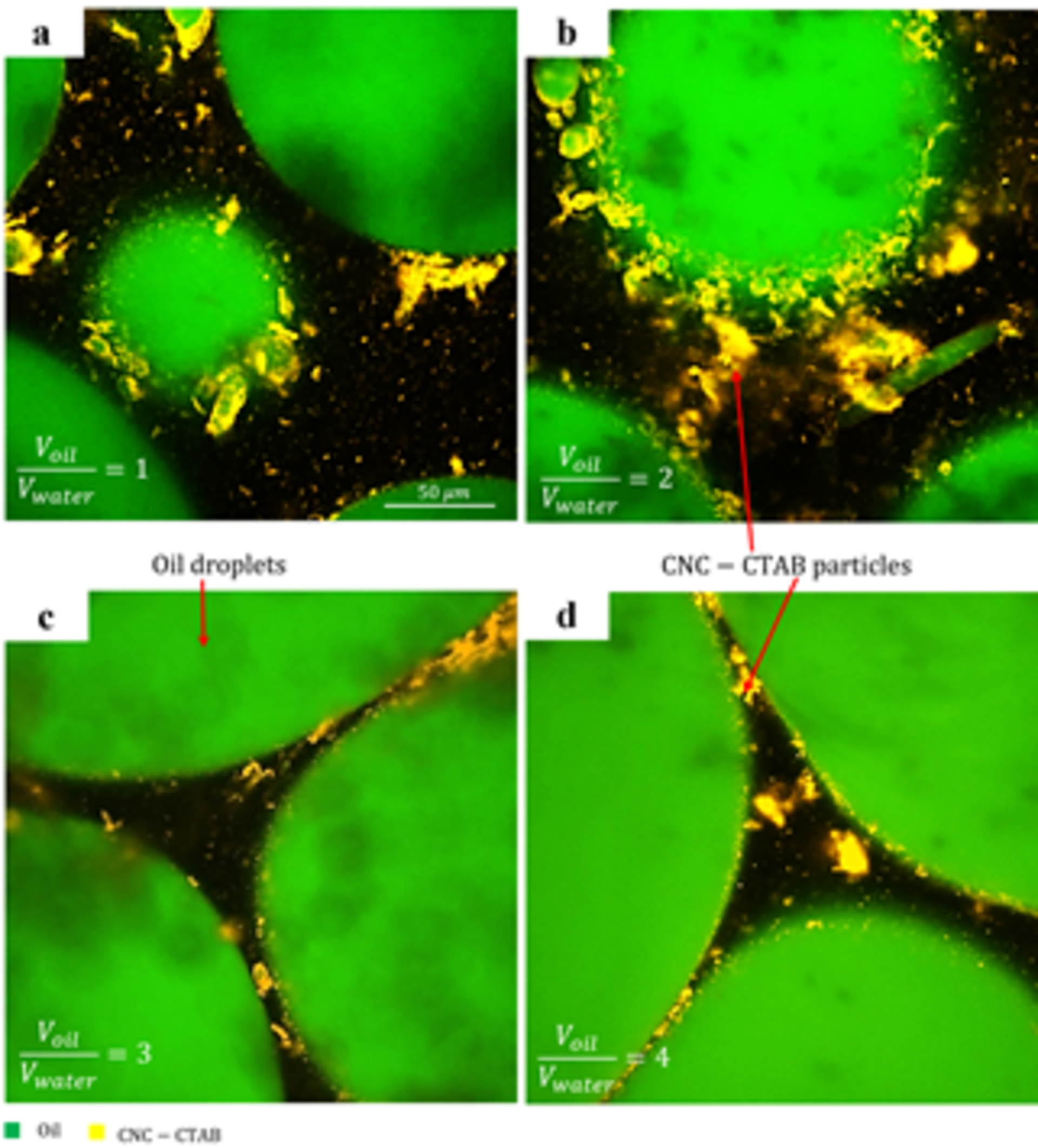
CNC-CTAB stabilized viscous oil-water interfaces
We conduct low energy input emulsification experiments with CNC-CTAB dispersions and a high viscosity mineral oil sample (η = 135 mPa s ). Similar to the heptane systems, emulsions are not generated with pure CNC dispersions, and the generated emulsions with pure CTAB solutions are stable for less than an hour. Consistent with heptane system, dispersions with CNC ≥ 0.5 wt.% and CTAB ≥ 0.1 CMC form stable emulsions with the viscous mineral oil. Fig. 4a shows that the generated emulsions with these dispersions are highly stable, with less than 10% in emulsion volume reduction over 12 hours. Similar to the heptane case, the mineral oil droplets generated by shaking have an average radius of 200 μm. Fig. 4b shows the droplet size distribution and average droplet size of the generated medium internal phase emulsions (Voil/VWater of 1, 2, 3, and 4) with CNC 1.00 wt.%-CTAB 0.50 CMC dispersion.
Although the oil phase density, viscosity, and polarity may affect the oil-water interfacial properties, CNC-CTAB dispersions that formed stable emulsions with heptane produce stable emulsions with the high viscosity mineral oil, and both emulsions have close values of stability and average droplet size. Dispersions that generate stable emulsions have the maximum values of interfacial viscoelasticity at heptane-water interfaces. Therefore, one may suggest that the interfacial properties, measured for heptane-water interface, may also inform the conditions required for generating stable high viscosity oil emulsions, where a direct measurement of interfacial dilatational elasticity is not feasible. In fact, high values of liquid bulk viscosity may affect the response of interface to oscillations, hence, an accurate measurement of interfacial viscoelasticity in high viscosity oil systems seems to be challenging.
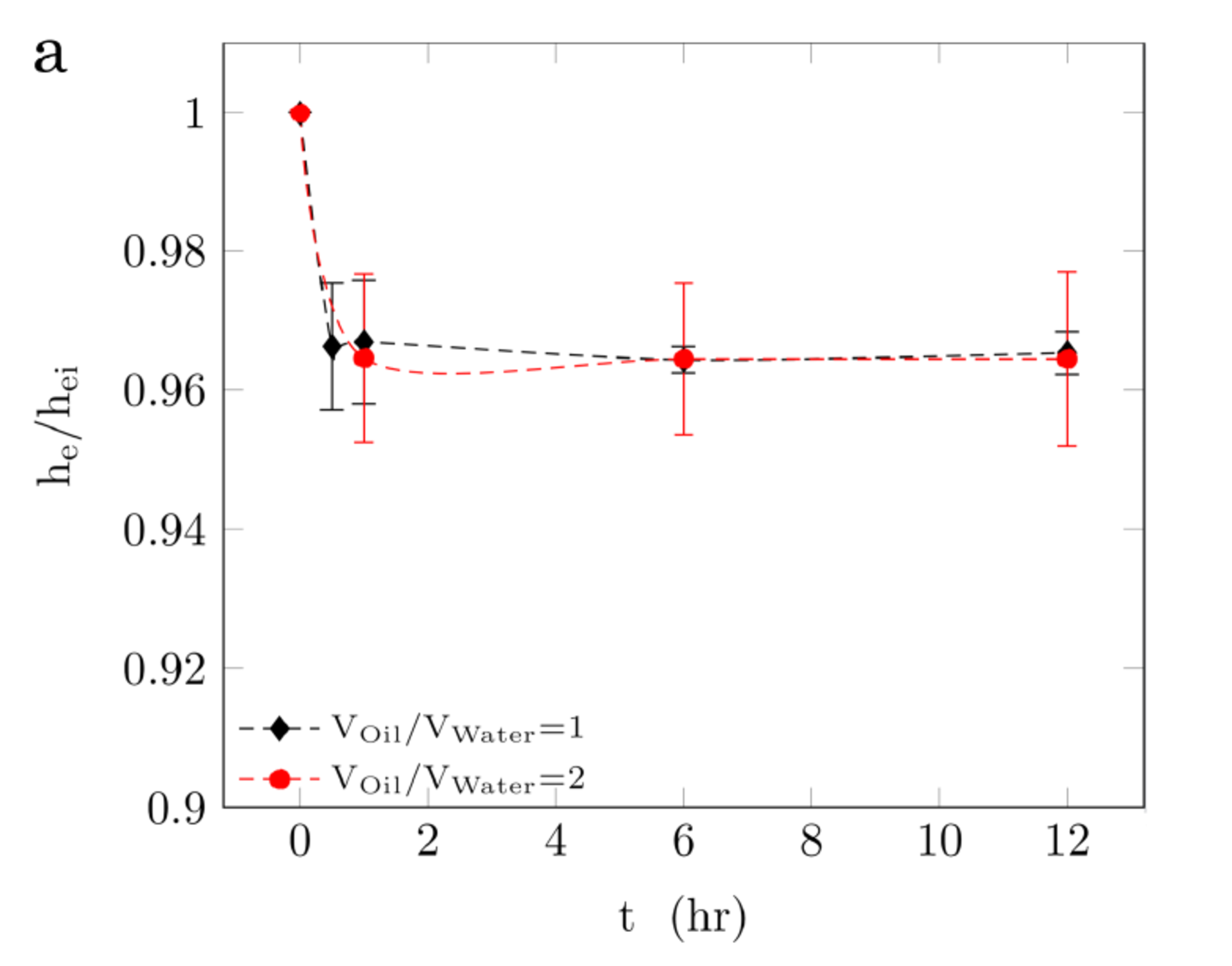
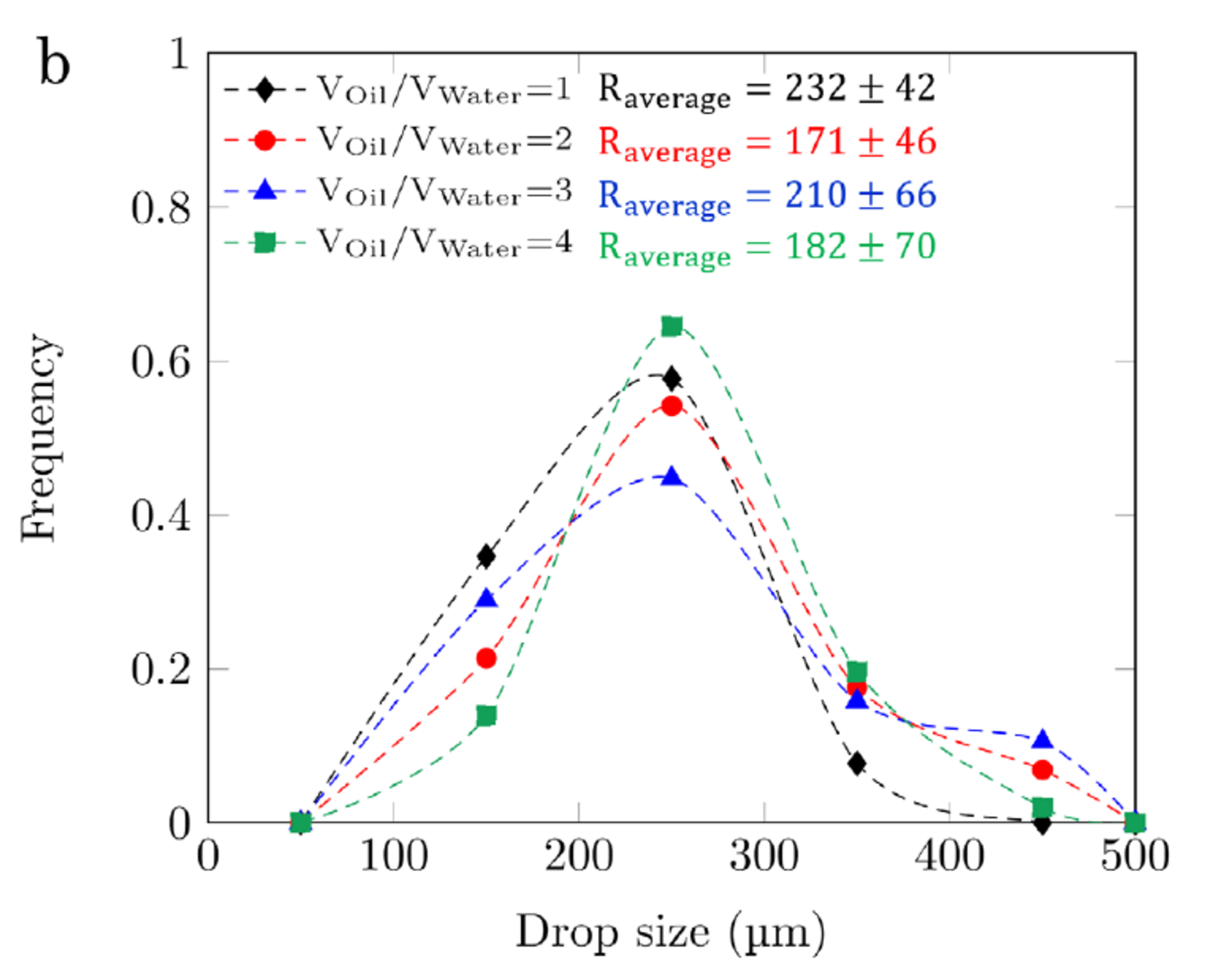
Summary
In this work we measure the interfacial rheology of surface-activated CNC particles at heptane-water interfaces. There is an optimum concentration of CNCs at which the interfacial viscoelasticity reaches the plateau, and its magnitude does not considerably increase by further increasing the surfactant-particle concentration. CNC-CTAB concentration above the optimum concentration generates stable medium internal phase oil in water emulsions with both heptane (representing low viscosity oil sample) and mineral oil (representing high viscosity oil sample), using low input energy emulsification technique. Thus, interfacial viscoelasticity data can be used as an indicator for emulsion formation and stability and we can extend our finding to a sample of mineral oil with a viscosity three orders of magnitude greater than heptane.
Literature
- (1) Cherhal, F.; Cousin, F.; Capron, I. Structural description of the interface of Pickering emulsions stabilized by cellulose nanocrystals. Biomacromolecules 2016, 17, 496−502.
- (2) Hu, Z.; Ballinger, S.; Pelton, R.; Cranston, E. D. Surfactant- enhanced cellulose nanocrystal Pickering emulsions. J. Colloid Interface Sci. 2015, 439, 139−148.
-
(3) Fuller, G. G.; Vermant, J. Complex fluid-fluid interfaces: rheology and structure. Annu. Rev. Chem. Biomol. Eng. 2012, 3, 519−543.
-
(4) Fuller, G. G. Rheology of mobile interfaces. Rheol. Rev. 2003, 77− 124.
-
(5) Bazazi, P.; Hejazi, S. H. Cellulose Nanocrystal Laden Oil–Water Interfaces: Interfacial Viscoelasticity, Emulsion Stability, and the Dynamics of Three-Phase Contact-Lines. Industrial and Engineering Chemistry Research. 2021, 60(13), 4892-4902.
We thank the authors for this scientific article and their consent to publish it at KRÜSS.