Dewetting
Dewetting describes the reduction of the contact area between a surface and a second, condensed (liquid or solid phase). This article refers to the most common case of dewetting between a solid substrate and a liquid. The reverse process is called wetting.
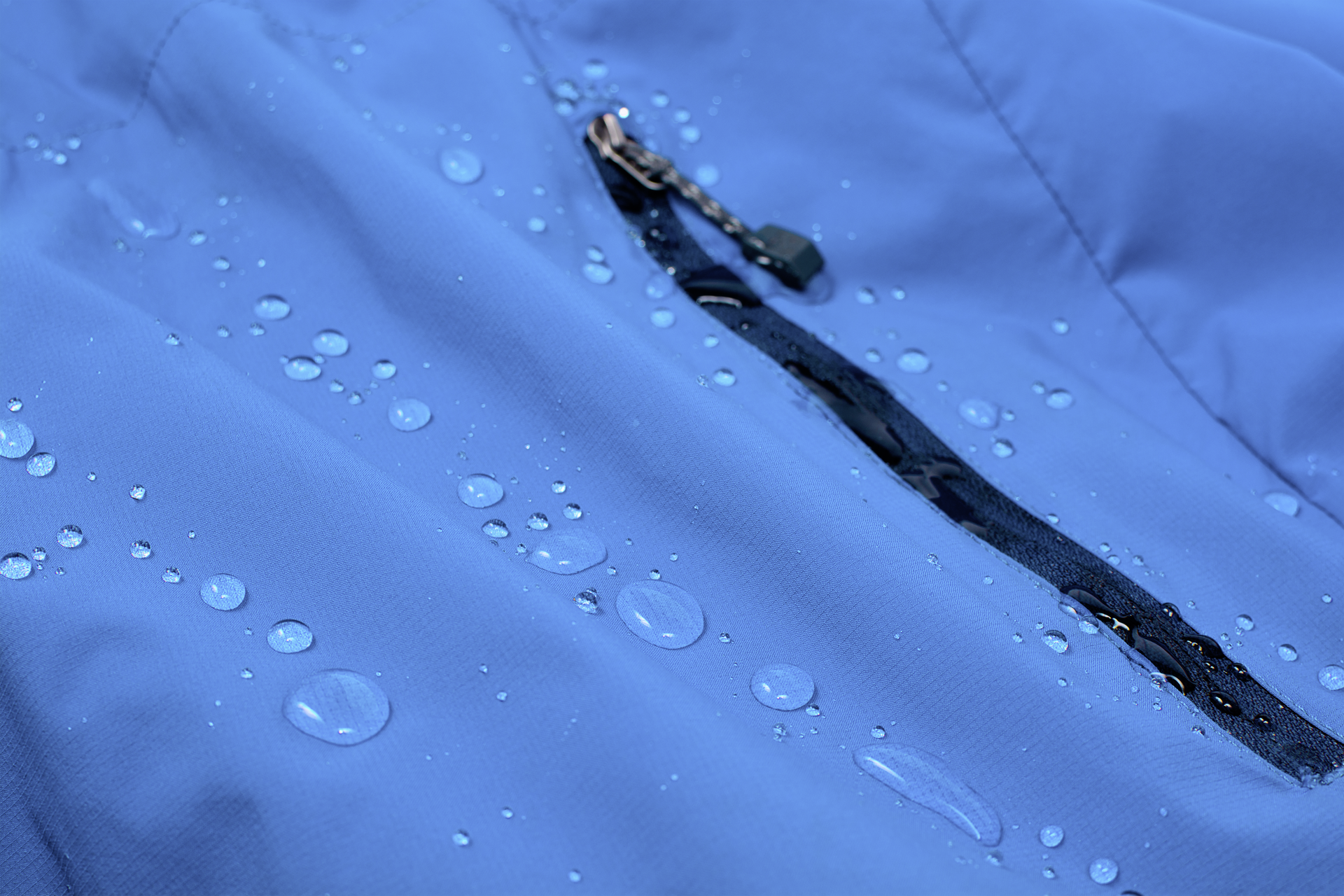
How are wetting and dewetting related?
While adhesive interactions between adjacent phases cause an enlargement of the interface, i.e. wetting, cohesive forces of the individual phases hold them together, so to speak, and act in the direction of minimizing the contact area (dewetting). In the equilibrium between these forces, which is described for ideal surfaces by Young's equation, a characteristic contact angle is formed.
Are wetting and dewetting energetically equivalent and only the direction is reversed?
Due to surface properties such as roughness or chemical inhomogeneity as well as the formation of an adsorption layer of the wetting phase on the substrate, the wetting and dewetting processes are not symmetrical. The receding angle that forms during or after a reduction in the contact area characterizes the dewetting. This can differ significantly from the advancing angle during or after a spreading movement. The difference between the receding angle and the advancing angle is referred to as hysteresis, or more precisely contact angle hysteresis.
Where does dewetting occur in practice?
In the case of materials that are not completely wetted (contact angle > 0°), there are hardly any natural or technical wetting processes that take place entirely without dewetting, i.e. a subsequent retraction movement. This is due to the usually highly dynamic nature of wetting, whether in the case of impinging raindrops or technical coating processes. The Wikipedia entry [June 12, 2024] defines dewetting as follows: Dewetting describes the process of retraction of a fluid from a non-wettable surface it was forced to cover. After wetting forced by dynamics, the spread of the contact surface is followed by a subsequent retraction.
Dewetting is therefore a common phenomenon that also occurs, for example, when raindrops run off a pane of glass or a leaf, or when gas bubbles grow during electrochemical processes. Last but not least, the evaporation of an incompletely wetting phase also causes dewetting.
Can dewetting and wetting be measured separately?
The Stood-up Drop method works with a deliberately high dosing dynamic of a drop of water and ensures that the liquid spreads out flat and then contracts into a defined drop in fractions of a second. This process is highly reproducible and results in a reliable measured value for dewetting, which is referred to as the recently receded contact angle (RRCA).
In order to measure wetting in isolation, the dosing dynamics are kept as low as possible to prevent initial spreading of the contact area. Liquid Needle dosing technology, for example, is suitable for this, with which the recently advanced contact angle (RACA) is measured. Advancing and receding angles can also be measured with conventional needle dosing systems, although the measurement takes considerably longer, and the results are more dependent on user decisions.
Advancing and receding angles as well as hysteresis can also be measured mechanically on the basis of capillary force using the Wilhelmy method of a tensiometer.
For which questions is it interesting to characterize dewetting?
Wettability analyses are well established in both R&D and quality assurance. The relevant contact angle results are easily accessible, anchored in many standards and linked to the surface free energy via Young's equation.
More recently, however, attention has also turned to measurements of the receding angle as a complementary, empirical method. It has been shown that the RRCA measured with the Stood-up Drop often correlates well with parameters of material pretreatments or with QC test results of surfaces. Examples of this are plasma treatments for surface activation, crosshatch tests for coating stability, or measurements of the moisture vapor transmission rate (MVTR), a key figure for moisture protection or breathability.
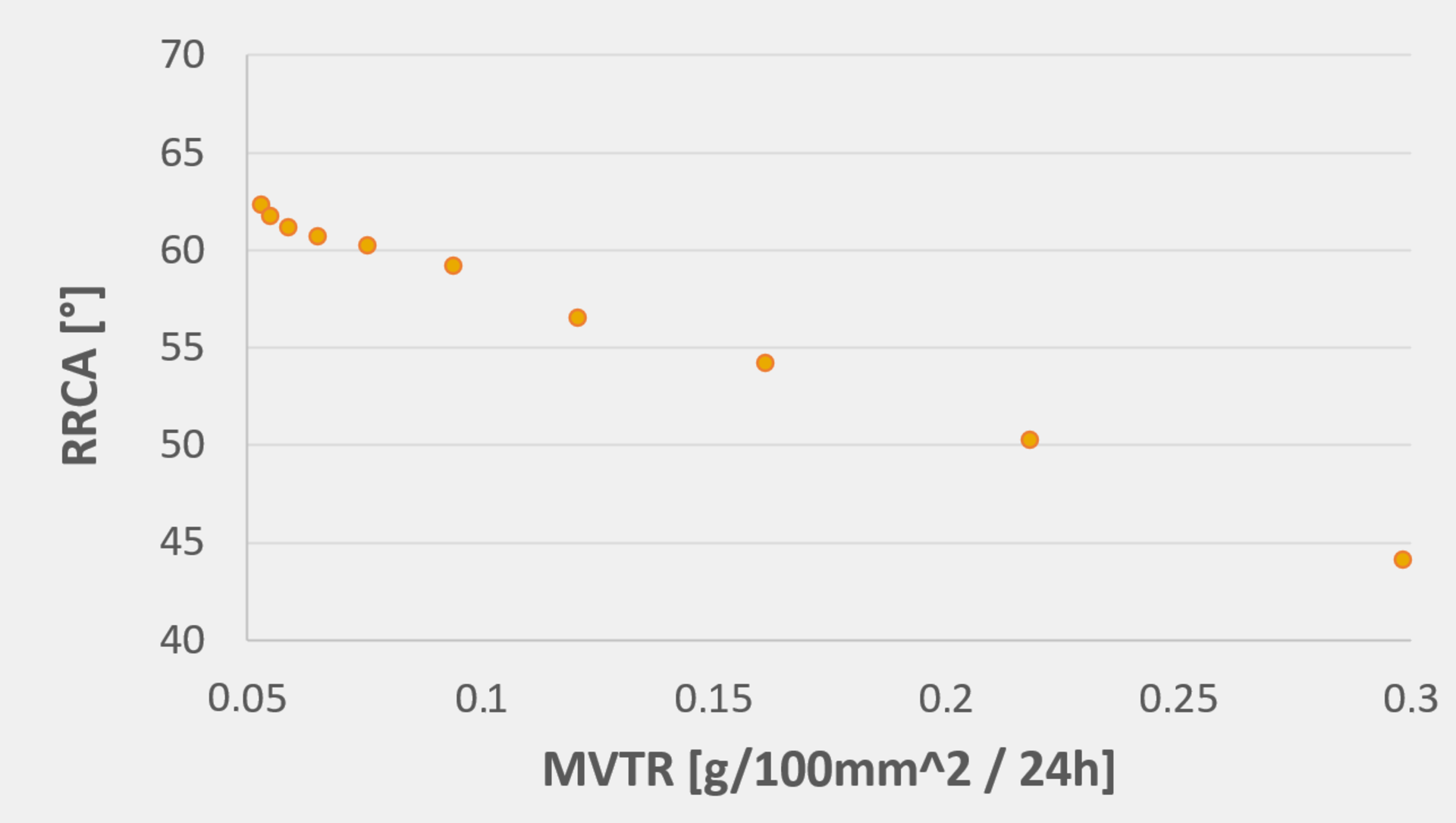
The focus here is not on analyzing the chemo-physical properties of the material, but on testing it on the basis of a previously determined calibration curve between the corresponding parameter and the RRCA. The quick and simple measurement of the RRCA has the potential to reduce the number of more complex prescreening tests or even replace such test methods altogether.