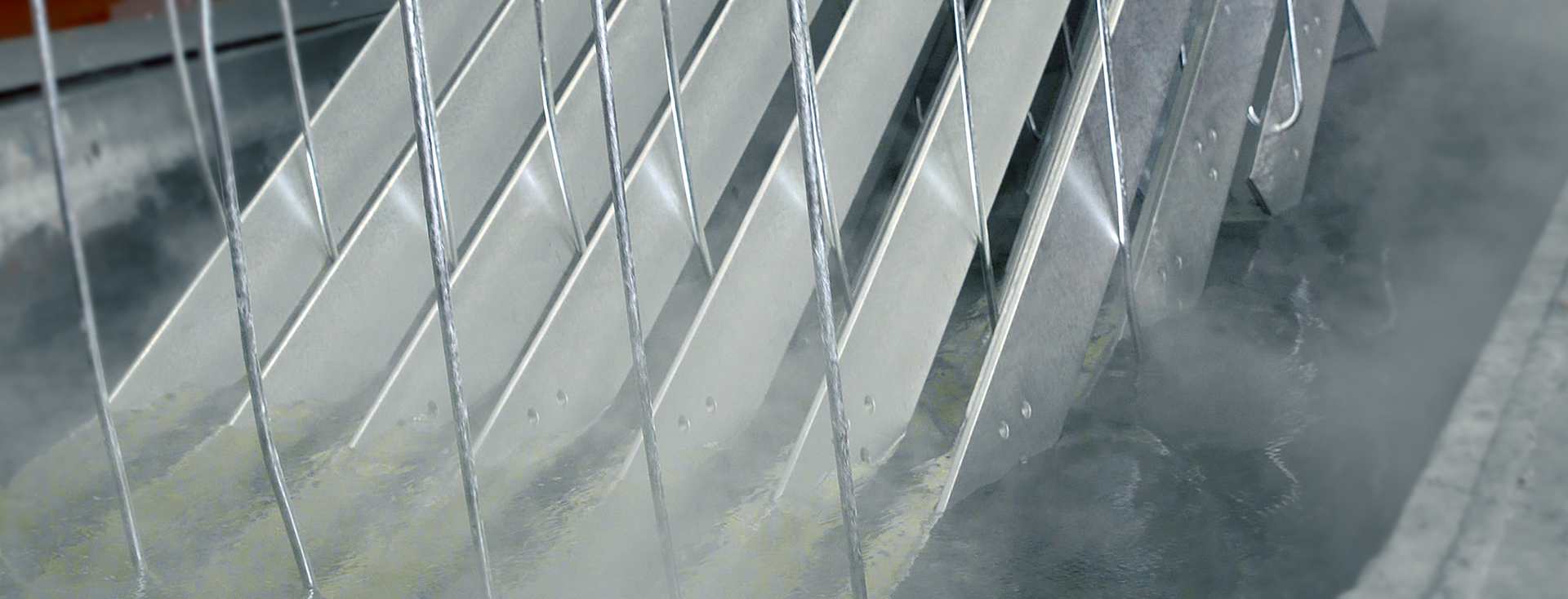
Determine how clean surfaces are: Quickly and on the go
Optimizing residence times in cleaning baths
Time is money, and that's also the case with industrial cleaning. Surfaces need to be cleaned until they have reached the necessary degree of cleanliness–and not longer. But how can the cleanliness of a surface be measured reliably? We cleaned steel plates of varying lengths in an ultrasonic bath and determined the respective surface free energies (SFE). What can't be seen by the naked eye was able to be made visible in this way: After 120 seconds, the optimum degree of cleaning was reached; any longer waiting time had no additional influence on the SFE of the steel plate samples. Once optimized, the success of the cleaning process could be checked in an instant with one-click measurements with either an “OK” or “not OK” result.
Background
Making contamination measurable
Basic cleaning of surfaces is a requirement for a multitude of processes, such as coating, painting, and bonding. If contamination remains on the surface, this results in faulty coating, visual paint defects and poor adhesion.
There are various methods available to measure the cleanliness of a surface, which could for example be based on fluorescence or even the use of X-rays. The disadvantage of these methods include limiting the verification of certain types of contamination, the influence of the distance of the sensor on the results or even simply the high costs of the instruments combined with laborious measurements costs.
One method that reacts with a high degree of sensitivity even to minimal contamination is the contact angle measurement. According to Young's Equation, the shape a drop will take on a surface is determined based on the surface tension of the liquid applied and the SFE of the sample surface (Fig. 1 A). Insoluble contamination (grease, oils, etc.) create a surface with low SFE, which leads to a larger contact angle (Fig. 1 B). Contamination active on the interface (surfactants, etc.) dissolve in drops and lower the surface tension, which is expressed in a time-dependent lowering of the contact angle (Fig. 1 C).
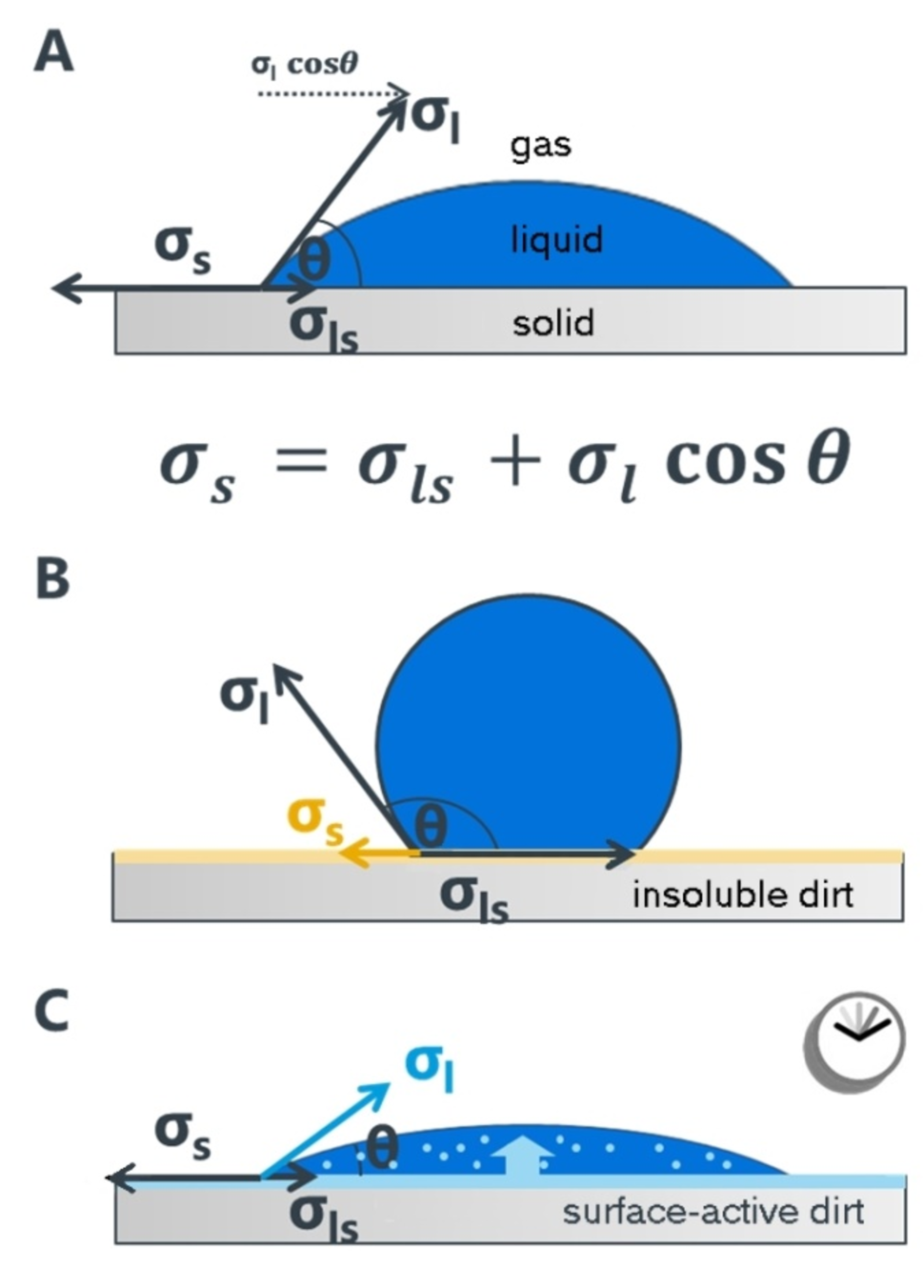
This method has the advantage of providing you with position-related information about the type of impurity (soluble/insoluble) and is easy and quick to apply. It is non-invasive and can be performed anywhere with a mobile device.
Testing
Steel plates (see Fig. 2) were cleaned at various treatment durations in an ultrasonic bath (made by Elma, Elmasonic S10H, frequency 50/60 kHz) filled with a 3% Mucasol® solution. After cleaning, the SFE of the steel plate was determined according to the OWRK calculation method using the Mobile Surface Analyzer – MSA [1], [2], [3]. Depending on the treatment duration, 4 steel plates were examined, and five drops of 2 µL per test liquid and plate were applied and measured. Both the cleaning and the measurements were performed at 30 °C. The liquid parameters are listed in Table 1.
Test liquid | σd [mN/m] | σp [mN/m] |
---|---|---|
Water | 21.8 | 51.0 |
Diiodmetahne | 50.8 | 0.0 |
Tab. 1: Test liquids used and their surface tension σ taking dispersive (d) and polar parts (p) into account based on OWRK.
Results
Fig. 2 shows example steel plate samples after increasing cleaning duration in the ultrasonic bath. Visually an effect can only be seen after very long cleaning periods.
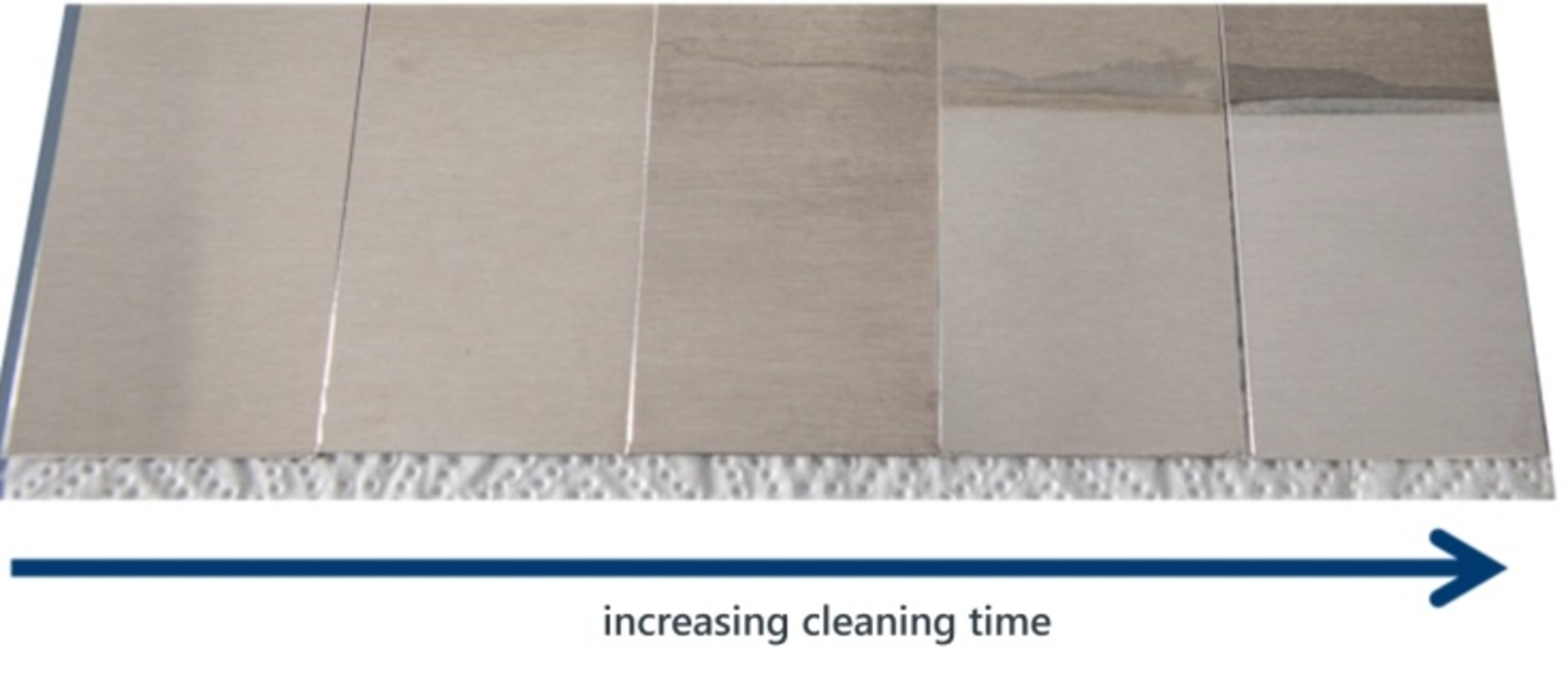
In the samples examined, the water contact angle dropped from the original 90° for the uncleaned samples to down to 13° for the cleaned samples. This indicates soiling that is not water-soluble.
Fig. 3 shows the SFE results of the steel plate samples examined. Here, even after only 10 seconds of cleaning, a significant increase in the SFE was observed, particularly for the polar part. After a cleaning time of 120 seconds, the maximum SFE is reached, and an additional increase of the cleaning duration has no additional effect. Based on this, a time of 120 seconds can be defined as the optimum cleaning duration.

Based on these results, a simple procedure can then be defined for routine one-click measurement in quality control which can be used as an OK criteria, for example a polar part of the SFE >30 mN/m
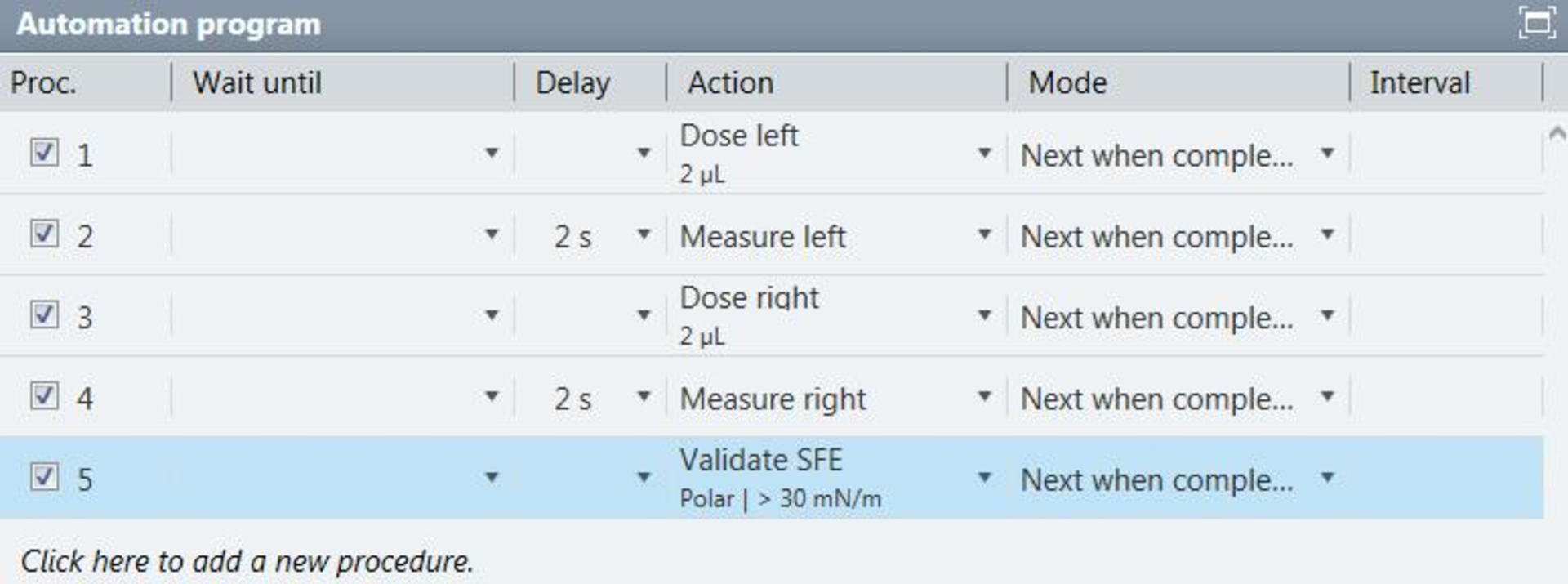
If this is lower, then the user will get a “Not OK” result and can take appropriate measures.
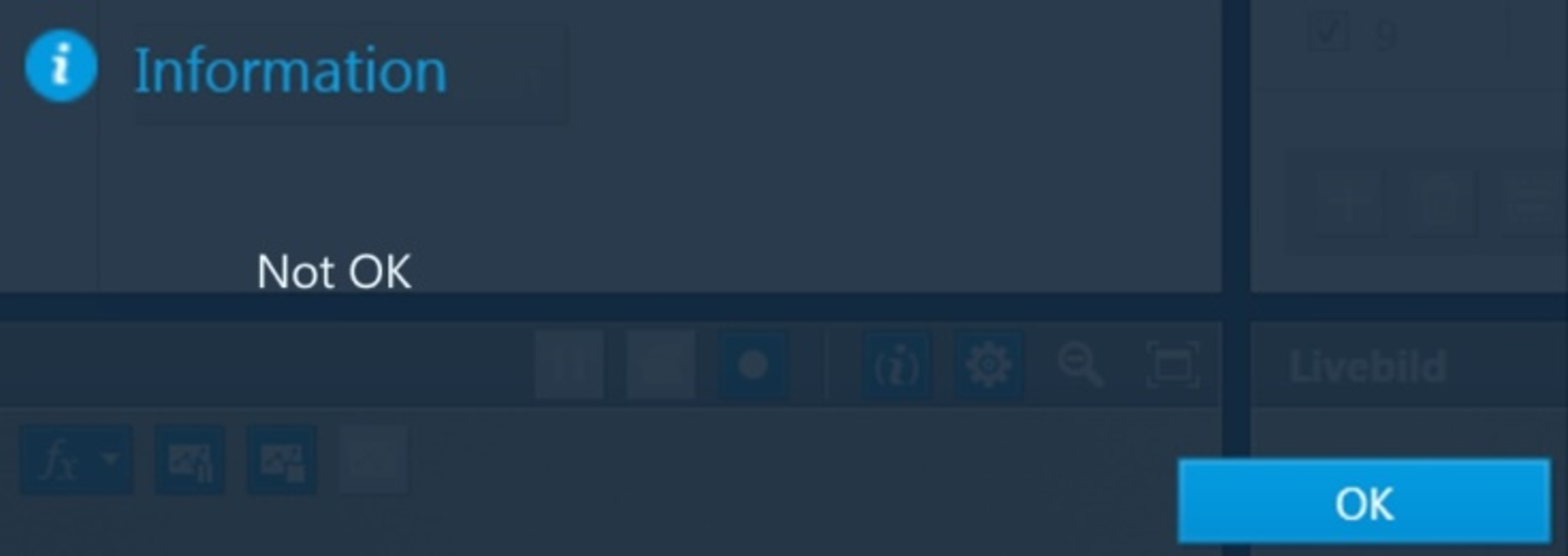
Summary
In the example of steel plate samples, it was shown how lightning-fast, simple and also mobile contact angle measurements were able to optimize the treatment time in a cleaning bath. Contamination that is invisible to the naked eye can be verified on the samples based on the measurement parameters of the surface free energy and can be identified as water-insoluble contamination (for example, oils). After the cleaning duration has been optimized, the success of the cleaning can easily be checked with a simple click as a part of process control.
Bibliography
- [1] D. H. Kaelble, Dispersion-Polar Surface Tension Properties of Organic Solids. In: J. Adhesion 2 (1970), P. 66-81.
- [2] D. Owens; R. Wendt, Estimation of the Surface Free Energy of Polymers. In: J. Appl. Polym. Sci. 13 (1969), P. 1741-1747.
- [3] W. Rabel, Einige Aspekte der Benetzungstheorie und ihre Anwendung auf die Untersuchung und Veränderung der Oberflächeneigenschaften von Polymeren. In: Farbe und Lack 77, 10 (1971), P. 997‑1005.