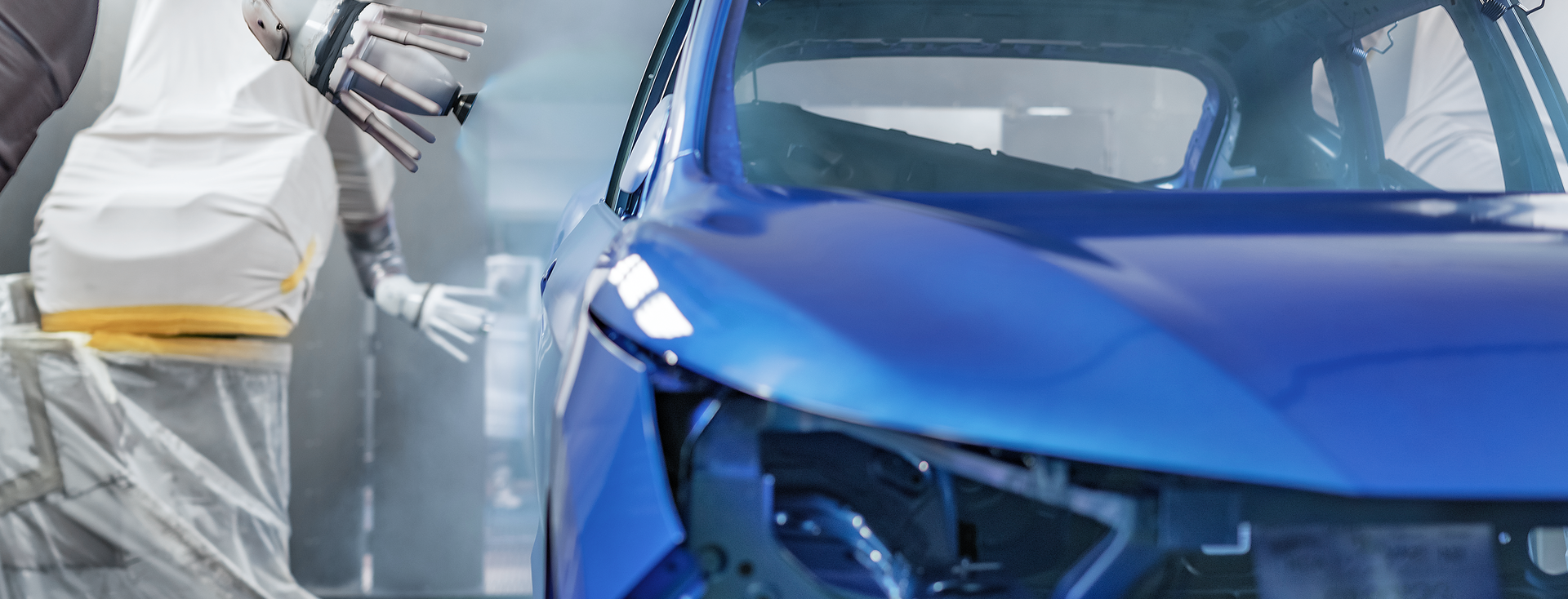
Predicting coatability
Contact angle and surface tension results as a basis for targeted development of coating formulations
Authors: Dr. Andrew Mellor (KRÜSS), Petra Della Valentina (BYK-Chemie)
An effective and reliable method for assessing and predicting coating performance is of critical importance in new material development/quality control. Particularly in the case of multi-layer systems, careful fine-tuning of individual components is essential to achieving good wetting and therefore coatability. With suitable measurement methods, it is possible to predict the behavior of multi-layer systems in regards to coatability. Such methodology is an indispensable tool for guiding additive selection, and significantly reduces the time and cost associated with (re)formulation.
In this study, contact angle and surface tension measurements of an automotive primer (cured) and basecoat (liquid), respectively, were used to form a complete description of the coating/substrate system. The presented analysis includes values calculated from the aforementioned measurements, i.e. surface free energy, (with polar and disperse fractions), work of adhesion, spreading coefficient, interfacial tension, and "wetting envelope". The results show how a polyether macromer-modified polyacrylate additive was used to optimize substrate coatability.
Background
Interest in producing higher-value, ‘smart’ materials has grown intensely over the last decade [1-3]. During production of such materials, functional coatings are often used to selectively enhance certain properties, or even allow for situational responses. Due to this, a wide range of coatings have been developed for many applications including self-cleaning, anti-corrosion, anti-microbial, anti-friction, environmentally friendly, super-hydrophobic/hydrophilic and oleophobic/oleophilic to name just a few. In recent times every-day items that incorporate multiple functional coatings into their design have become increasingly common [4]. As the complexity of these multi-layer composites increases, so does the challenge in ensuring compatibility between each coating. As all layers are interconnected (either directly or indirectly) it is often helpful to consider the so-called “chain of compatibility” in the final product.
In industry, different coatings are usually obtained from different suppliers and are often designed on different bases, i.e. water-based vs solvent-based. Therefore, additives are frequently used to optimize properties and maintain the chain of compatibility.
The structure of multi-layer coatings
Determining the most appropriate additives to use, in the correct amounts, can be tricky and usually involves a time-consuming trial and error process. Utilizing suitable measurement methods makes it easier to predict wetting behavior and coatability, thereby significantly reducing cost and time required to reformulate.

In the automotive industry, multi-layer coating systems are standard, and have been commonplace for some time. In the classic example (see Fig.1), a cathodic dip coating (CED coating) is first applied to a bare steel component. Then, a primer is added, followed by a pigmented base coat (to achieve the desired coloring. Finally, a clear coat creates the expected finish (gloss, flow, ware resistance, texture etc.) [5]. In the case of primer/basecoat compatibility, an increase in surface free energy of the cured primer is often required to facilitate good coatability. Traditionally this has been very difficult to achieve, however, recent developments show this can be resolved using polyether macromer-modified polyacrylates [6].
Surface-analytical parameters that describe compatibility between coating layers
The basis for good coatability is the wetting behavior of the two layers (i.e., substrate - liquid system). In this work, surface tension (SFT) and contact angle measurements of the coating and substrate, respectively, are used to form a complete description of the system. This also includes values calculated via the aforementioned measurements including surface free energy (SFE), with its polar and disperse fractions, work of adhesion (WoA), spreading coefficient, interfacial tension (IFT; frequently referred to as “interfacial energy”), and "wetting envelope".
Much attention has been paid to the assessment of coatings in relation of adhesion, that is, the tendency of a coating and substrate to remain in contact with each other. For this, it is commonplace to look to the WoA between the substrate and coating. Coatability describes the relative ease of which a substrate can be coated by a liquid. Much like adhesion, the ability to quickly and easily assess substrate coatability is a vital tool for the development and formulation of coated materials.
WoA describes the balance of forces acting at the interface, namely SFT, SFE and IFT. SFT and SFE can be described as a measure of how unfavorable increases in surface area are for liquids and solids, respectively. Therefore, WoA can be considered a measure of how strongly the two phases at an interface oppose separation. In this way, IFT represents the reduction of this opposition as a result of any mismatch in the chemistry of the two materials, i.e., their polar/non-polar ratios. In other words, a higher WoA tends to indicate lower chance of delamination at an interface [7].
As WoA essentially describes the likelihood of a coating delaminating from a surface, this value is commonly used as a predictor of coating performance in general. This approach often works well, however there are limitations. Specifically, WoA values tell us nothing about the size of SFT and SFE relative to each other.
Experimental part
Samples and their preparation
As solid samples, stainless steel plates were first coated with a typical automotive solvent borne primer. For two of three samples, the primer solution was modified by the addition of 0.1% vol. BYK-310 and 0.3% vol. BYK-3560, respectively. After being coated, each sample was cured in the open air for 20 min at 140 °C and then coated with a red water borne basecoat. The sample was applied by spray gun with a gradient from 0 µm - 20 µm in the dry coating thickness. This created a gradient effect, where basecoat thickness increases vertically down each sample from 0 µm to 20 µm. After basecoat application, all three samples were photographed, and the relative coating performance (coverage, distribution, coloration) was inspected visually.
Contact angle and surface tension measurements and their evaluation
After curing of the primer, but before application of the basecoat, contact angle measurements were performed on each sample using a KRÜSS DSA100 with 5 different test liquids from polar to non-polar. SFE properties, including polar (p) and disperse (d) components of the solid (s) and liquid (l), were subsequently calculated according to the OWRK model [8-10]:

where σls, σl, and σs express the IFT, SFT, and SFE, respectively.
The total static surface tension of the basecoat was determined by a KRÜSS Force Tensiometer – K100 via the Du Nuöy ring method.
Following this, a KRÜSS Drop Shape Analyzer – DSA100 was used for contact angle measurements of the same basecoat on a flat, homogeneous, non-polar substrate of known SFE (PDMS – Sylgard184). In the thus provided absence of polar interactions, the OWRK model can be simplified to yield the non-polar fraction of the basecoat’s SFT. Subsequently, the polar surface tension component was then calculated via the simple relationship

where σtotal, σp, and σd denote total, polar, and disperse SFT components, respectively.
All the above-mentioned determinations of SFE and SFT were performed automatically by the KRÜSS ADVANCE software in sessile drop mode.
Using SFE and SFT as an input, the Adhesion Analysis tool of the ADVANCE software automatically computed values and iso plots for work of adhesion (WoA), interfacial tension (IFT), spreading coefficient (S), and theoretical contact angle of all given coating/substrate combinations.
Results
Visual assessment of SFE/SFT results for Control sample and BYK-310
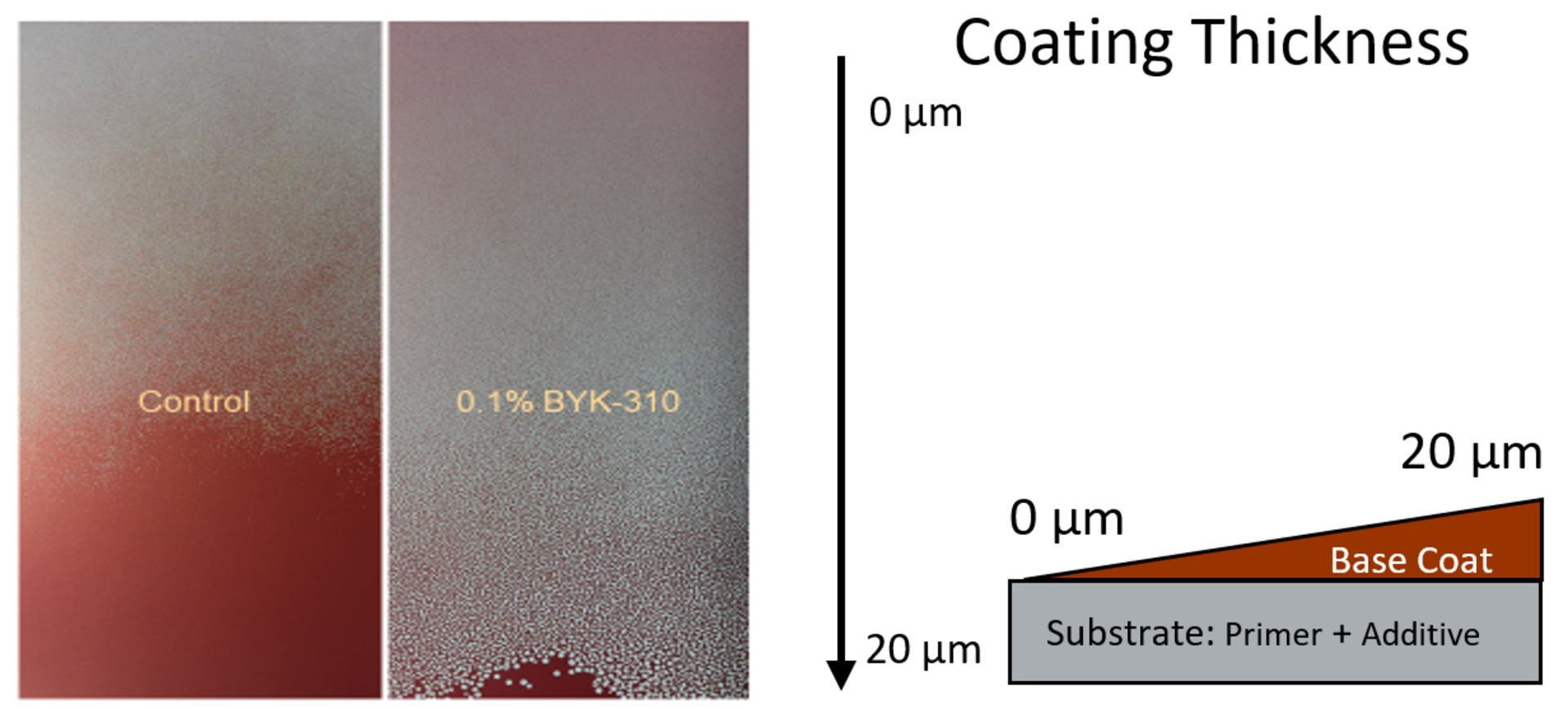
To investigate relative performance of the primer additive BYK-310 with a specific basecoat formulation, test panels were made by applying a standard primer both with (BYK-310) and without (Control) additive to a steel substrate. Following application, the primer was cured to form a solid substrate. The chosen (red) basecoat was then spray coated onto the now solidified primer layer. During application, basecoat thickness was varied from top (~0 µm) to bottom (~20 µm) for each sample.
On visual inspection of the fully coated test panels (see Fig. 2) it is immediately obvious that addition of 0.1% BYK-310 has a detrimental effect on coatability of this specific primer formulation, even at relatively high coating thickness. It is worth noting, in this case coatability is related to the performance of the specific primer/basecoat pair that was tested and is not expected to be universally true.
To better understand, and hence explain, the behavior at the primer/basecoat interface, the SFE of both cured primer layers, i.e. in the solid state, was determined via contact angle measurements, as well as the SFT properties of the basecoat (see Table 1).
Coating Data
Sample |
σtot [mN/m] |
σd [mN/m] |
σp [mN/m] |
Polarity (%) |
---|---|---|---|---|
Basecoat (Red) |
29.30 |
22.40 |
6.90 |
23.55 |
Substrate Data
Sample |
σtot [mN/m] |
σd [mN/m] |
σp [mN/m] |
Polarity (%) |
---|---|---|---|---|
Primer Control |
26.80 |
22.60 |
4.20 |
15.67 |
Primer + 0.1% BYK-310 |
25.40 | 20.20 | 5.20 | 20.47 |
Table 1: SFT (top) and SFE (bottom) data of the basecoat and two test samples, respectively. Polar (p) and disperse (d) components are also indicated, with overall polarity given in % [5]
Reviewing the values in Table 1, it is apparent that addition of BYK-310 has an almost negligible effect on total SFE of the cured primer. An often-used rule of thumb for assessing coating performance states, “if the total SFE of a substrate is equal to, or greater than, the total SFT of a liquid, then good wetting will be achieved.” Unfortunately, this rule of thumb is unreliable; indeed, in this case the difference in coatability of the two samples cannot be explained in this way. Both samples exhibit SFE values less than the SFT of the basecoat.
Using the data in Table 1, it is possible to differentiate between the two samples based on polar/disperse ratio, however, it is not immediately obvious from this which substrate will result in better performance. Hence, we can conclude that comparing SFT and SFE properties of a coating/substrate system are not sufficient for predicting coatability.
Further evaluation of adhesion related parameters for Control sample and BYK-310
Fortunately, SFT and SFE data alone is sufficient to calculate a whole range of higher-level parameters that allow us to build a more detailed picture of the substrate/coating interface, without the need to collect any further data. WoA, IFT, and spreading coefficient (S) are particularly relevant for assessing coating performance. Table 2 shows the calculated wettability parameters for the Control/Basecoat and BYK‑310/Basecoat systems.
Adhesion Analysis
Interface between basecoat and |
---|
|
Primer Control |
Primer + 0.1% BYK-310 |
WoA |
55.77 mN/m | 54.52 mN/m |
IFT | 0.33 mN/m | 0.18 mN/m |
S | -2.83 mN/m | -4.08 mN/m |
θ | 25.41° | 30.59° |
Table 2: Calculated WoA, IFT, S, and contact angle (theoretical) values for both Control/basecoat and BYK-310/ basecoat combinations. Images of each test sample are included below [5].
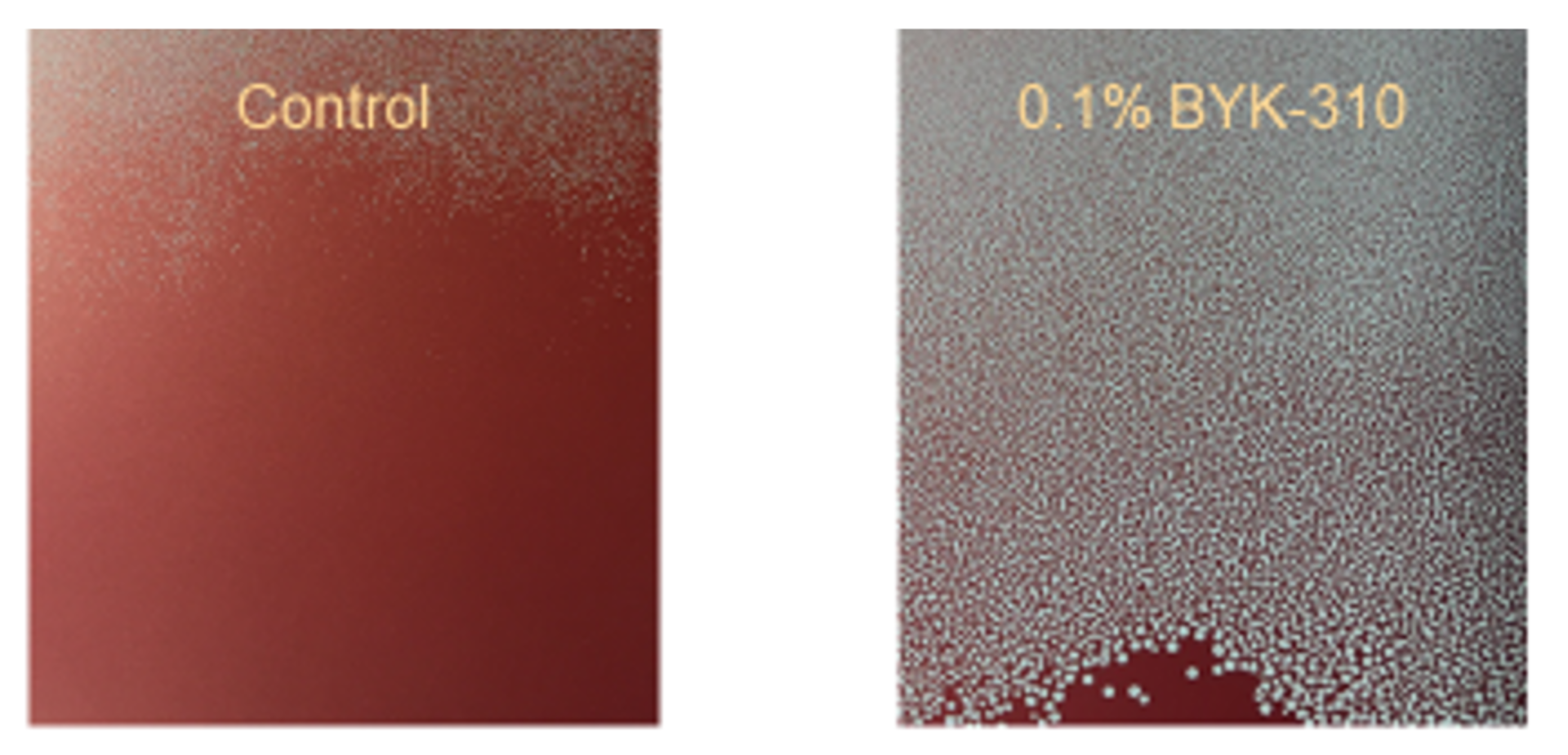
WoA values are often looked to as a method for characterizing general coating performance; however, this approach does have some shortcomings. This is apparent when comparing the WoA values of the two primer/basecoat systems (see Table 2). While the trend in WoA does agree with the observed coatability, the values differ by just 2.3%. From this analysis one can expect both systems to perform similarly in terms of adhesion, but clearly this tells us nothing about the relative coatability of the two substrates.
Additionally, while IFT values do show a more significant difference between the Control and BYK-310 samples, the trend is in the wrong direction, i.e. the IFT of the Control system is higher (indicating worse compatibility) than that of BYK-310. It is worth noting that in the automotive industry an IFT value of less than 1 mN/m would be considered acceptable, as is the case for both samples.
Spreading coefficient as a reliable predictor of coating performance
The spreading coefficient of a coating/substrate system is commonly overlooked as an indicator of coating performance. However, in this case S values for the two systems seem to follow the observed coatability well, both in terms of the overall trend and relative difference (-144% on addition of BYK-310). This perhaps should not be too surprising when considering what S represents.
Unlike WoA, S is a direct measure of how forces that are beneficial to wetting (SFE) balance against those that are detrimental to wetting (SFT, IFT). In many ways, this can be thought of as a quantitative version of the aforementioned rule of thumb, i.e. “if S is greater than zero, then good wetting will be achieved”. The benefit of calculating S over a direct comparison of SFE and SFT is that here the balance of adhesive and cohesive work at the interface, as well as polar/non-polar ratios of each component, are automatically taken into consideration. On this basis, we consider S can be used as an invaluable parameter for the evaluation of coating performance.
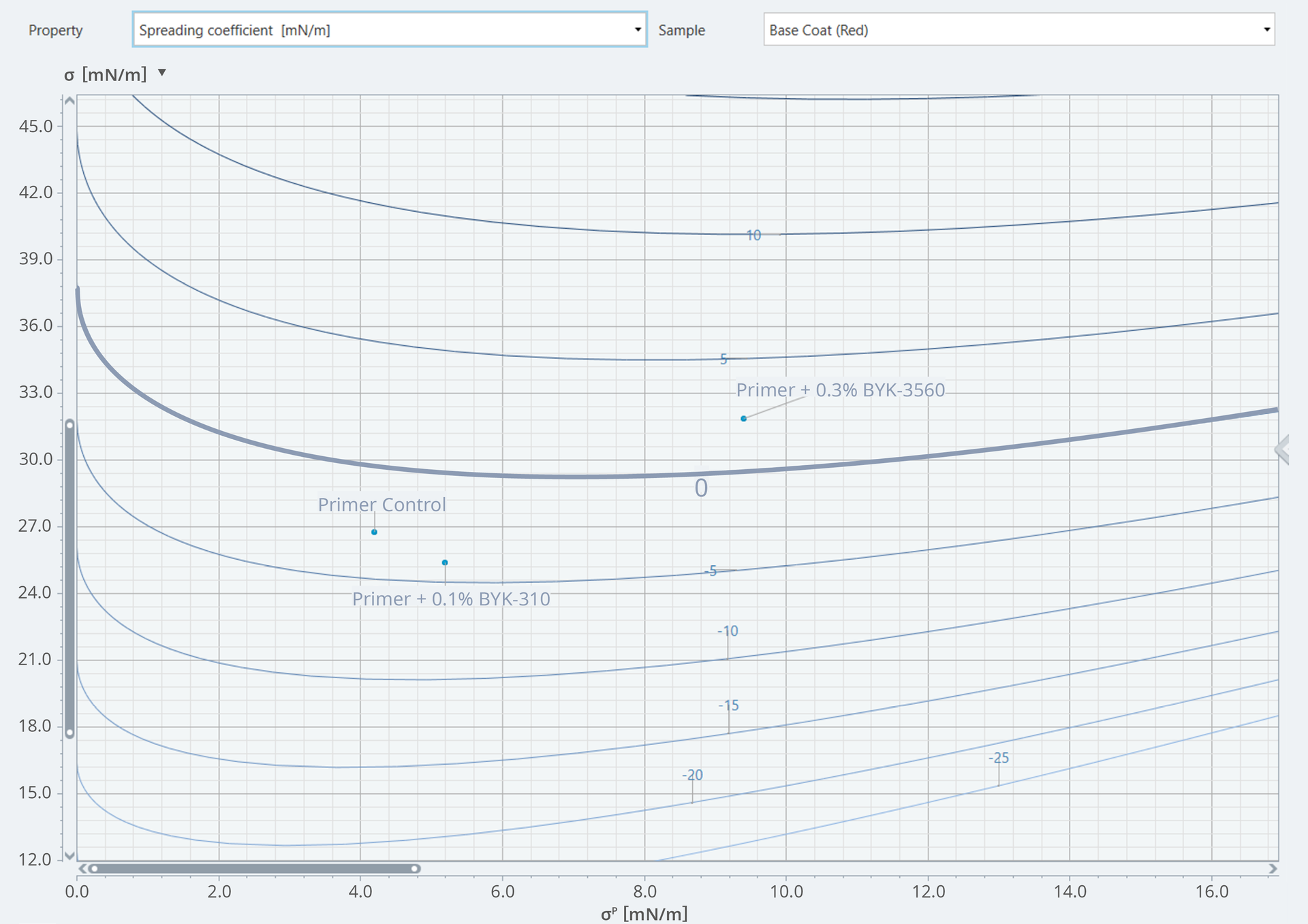
Typically, formulation/reformulation of a single coating can be a lengthy process involving many potential candidates. With this in mind, using an iso plot to represent the complete set of systems, relative to one another can be incredibly useful. By representing the information visually, the best candidates for further development can be easily identified. Fig. 3 shows such an iso plot for the spreading coefficient of the chosen basecoat for the Control and BYK‑310. From this visual layout, it is immediately apparent that Control sample has better performance in terms of spreadability, as it lies closer to the S=0 line. It is also possible to use such an iso plot to gauge the necessary alterations needed to improve coatability.
Analyzing a new formulation that was optimized using S as a guideline
Using the above investigation as a guide, a new primer formulation was developed. This time a polyether-macromer-modified polyacrylate additive, designated BYK-3560, was used in place of BYK-310. As all relevant data about the basecoat had been recorded previously, a full set of new data could be obtained simply by measuring the SFE of the new primer after curing.
Interface between basecoat and |
---|
|
Primer Control |
Primer + 0.1% BYK-310 |
Primer + 0.3% BYK-3560 |
WoA |
55.77 mN/m | 54.52 mN/m | 61.01 mN/m |
IFT | 0.33 mN/m | 0.18 mN/m | 0.19 mN/m |
S | -2.83 mN/m | -4.08 mN/m | 2.41 mN/m |
θ | 25.41° | 30.59° | 0.00° |
Table 3: Calculated WoA, IFT, S and θ (theoretical) values for all three test sample/basecoat combinations. An Image of each test sample is included below each column [5].
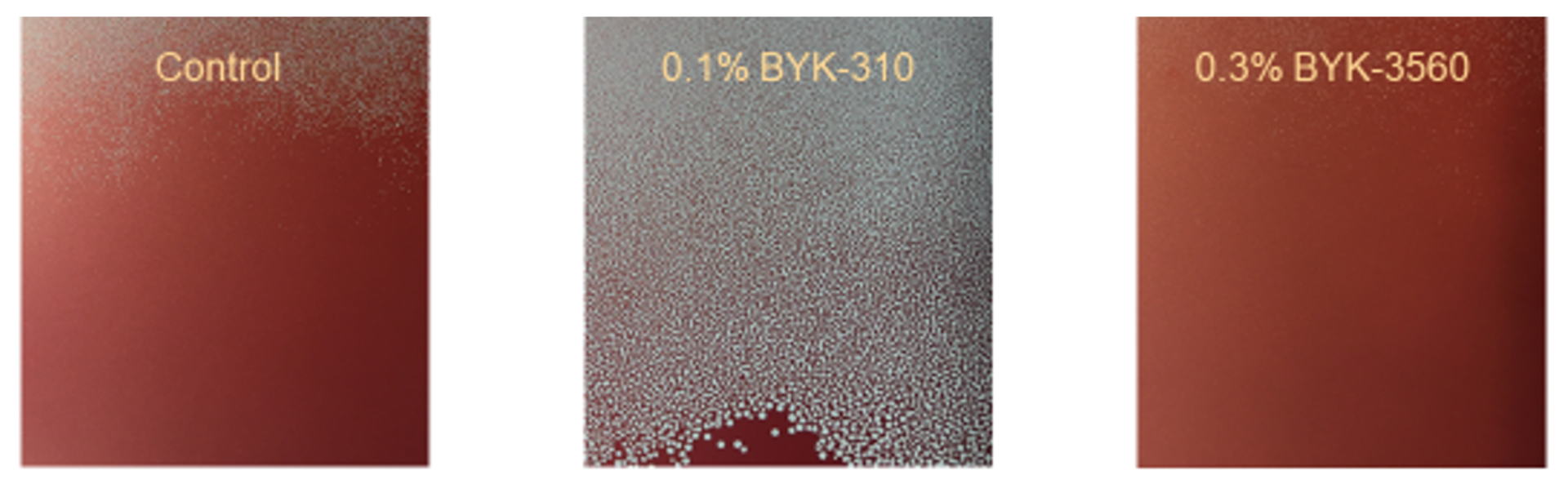
In comparison to the Control sample, the new BYK-3560 substrate showed a marked increase in total and polar SFE, while non-polar SFE remained more or less the same. Using the iso plot in Fig. 3, it is possible to estimate at a glance that such an increase in polar SFE will yield an S value approximately 200% greater than that of the Control system. Indeed, subsequent calculations of the various parameters showed that S increased by more than 185%. It is also worth mentioning that the WoA of this system was noticeably increased vs that of the Control and BYK-310 systems, indicating a greater coating/substrate adhesion for the chosen basecoat formulation. The IFT of the BYK-3560 system, while improved relative to the control, was very similar to that of the BYK-310 system.
After confirming the BYK-3560 substrate as a potential candidate for improved coatability with the basecoat, the cured substrate was then spray coated in the same way as the other samples. In this case, visual inspection of the sample reviled a greatly improved coating of the substrate, in line with the improved value of S. Most notably, the improved performance allowed for a more complete coating of the sample at lower coating thickness. This in turn necessitates the use of less basecoat overall, thereby improving the efficiency of the coating process and reducing costs.
Summary
Addition of 0.1% BYK-310 to an automotive primer revealed a significant visual reduction in coating performance (coatability) for a typical automotive basecoat. Using values derived from contact angle and surface tension measurements, the wettability parameters work of adhesion (WoA), interfacial tension (IFT) and spreading coefficient (S) of this system where determined, and a complete description of the coating-substrate system was generated. On comparison, neither WoA nor IFT were sufficient indicators of the observed coatability of the system with or without BYK-310. In contrast, the difference in S for the two samples was far more pronounced and provided a much clearer quantitative indicator of coatability.
Following the above analysis, a third formulation was tailored towards better performance with this specific basecoat, this time using a polyether-macromer-modified polyacrylate additive (BYK-3560). In this case, addition of 0.3% BYK-3560 resulted in greatly improved substrate coatability. Examining the wettability parameters of this system, a noticeable increase in WoA was observed following addition of BYK-3560, and most strikingly, S increased by 185% vs the Control sample. This in turn facilitated adequate coating of the substrate at lower base coat thickness. Use of a BYK-3560 containing primer was shown to be effective at improving coatability of a specific basecoat formulation over a typical automotive primer. As a direct result of the improved performance, visually acceptable wetting of the substrate can be achieved at lower basecoat thickness.
The work presented here demonstrates how adhesion analysis to be an effective tool to guide development of new primer/basecoat pairs or aid troubleshooting of coating issues in the future.
Abbreviations
IFT |
interfacial tension between a liquid and a solid |
S |
|
SFE |
surface free energy of a solid |
SFT |
surface tension of a liquid |
WoA |
Work of Adhesion |
Symbols
θ |
|
σl |
SFT of a liquid |
σs |
SFE of a solid |
σls |
IFT between a liquid and a solid |
Superscript d |
disperse part of SFE or SFT |
Superscript p |
polar part of SFE or SFT |
Bibliography
- [1] P. I. Dolez, J. Mlynarek, 2016, Smart Materials for personal protective equipment: Tendencies and recent developments, p.497-517, Woodhead Publishing.
-
[2] N. Shehata, M. A. Abdelkareem, E. T.Sayed, D. E. Egirani, A. W.Opukumo, 2021, Smart Materials: The Next Generation, Encyclopedia of Smart Materials, p. 1 – 12, Elsevier Inc.
-
[3] J. L. Hu, 2016, Active Coatings for Smart Materials, p. 1-7, Woodhead Publishing.
-
[4] J. J. Moore, D. Zhong, 2003, Advanced Coatings for Structural Materials, Encyclopedia of Materials: Science and Technology (2nd Ed.), p. 1-12, Elsevier Science Ltd.
-
[5] P. D. Valentina, Hamburg, 12/11/2019, Anwendungsbeispiele aus der Tensiometrie, BYK-Chemie GmbH.
-
[6] „BYK-3560 und BYK-3565 ausgezeichnet!“, www.altana.de, BYK-Chemie GmbH, 04/09/2018, https://www.altana.de/presse-news/artikel/byk-3560-und-byk-3565-ausgezeichnet.html
-
[7] S. Ebnesajjad, A. H. Landrock, 2015, Adhesives Technology Handbook (3rd Ed.), p. 19-34, William Andrew.
-
[8] D. H. Kaelble, Dispersion-Polar Surface Tension Properties of Organic Solids. In: J. Adhesion 2 1970, P. 66-81.
-
[9] D. Owens; R. Wendt, Estimation of the Surface Free Energy of Polymers. In: J. Appl. Polym. Sci 13 1969, P. 1741-1747.
-
[10] W. Rabel, Einige Aspekte der Benetzungstheorie und ihre Anwendung auf die Untersuchung und Veränderung der Oberflächeneigenschaften von Polymeren. In: Farbe und Lack 77,10 1971, P. 997-1005.
Acknowledgements
We would like to offer a special thanks to our partners at BYK for the data and images provided for this report and for their useful suggestions and continued cooperation.
Information about BYK is available here: www.byk.com.
BYK® is a registered trademark of the BYK group.
As mentioned in this application report, a K100 Force Tensiometer had been used for carrying out some of the measurements. The same measuring methods, only with improved precision and ease of use, can now be performed with the up-to-date Tensíío instrument.