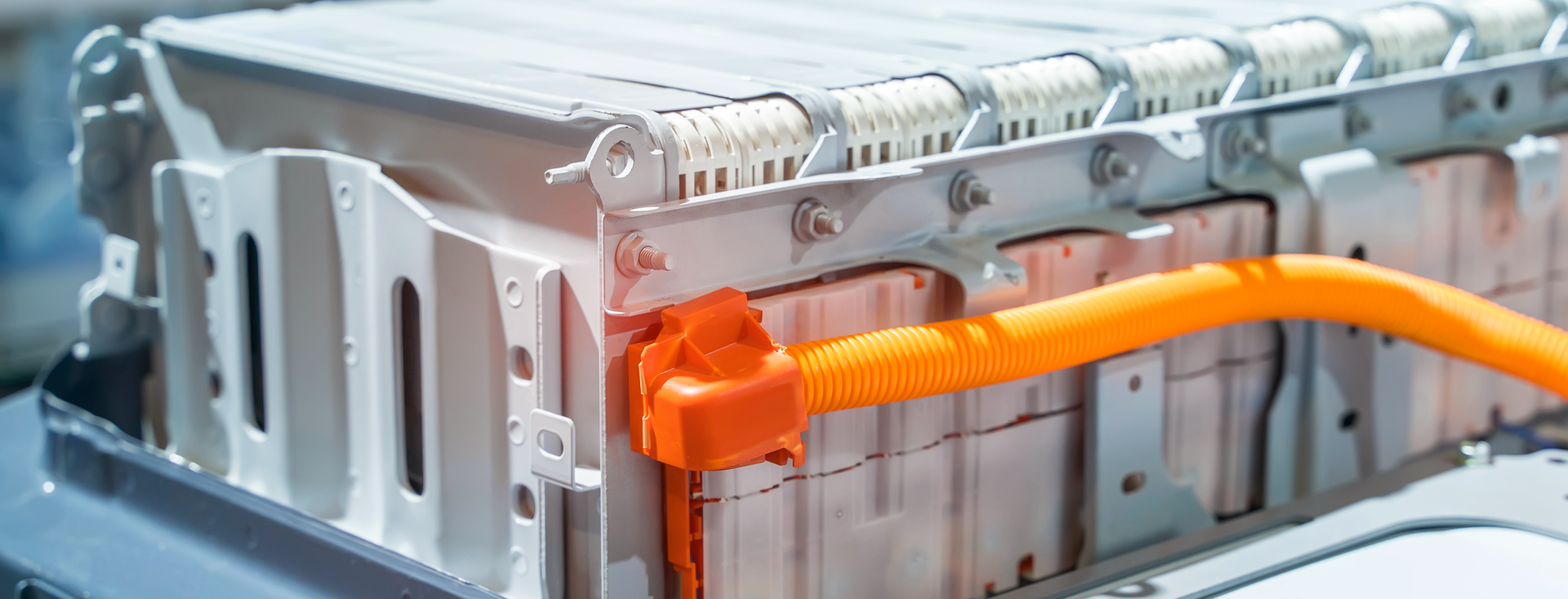
Wetting of battery electrodes
Speeding up a time-consuming process and optimizing calendering of electrodes with interfacial analytical methods
In any mass production process, time and cost efficiency are closely related. But while seconds are often at stake in the field of machine-based mass production, manufacturers of high-capacity lithium-ion batteries have to contend with time problems in completely different dimensions. It can take many hours to fill a cell with electrolyte - an annoying bottleneck in the process chain. Battery developers are therefore desperately looking for ways to optimize production steps such as calendering and speed up the wetting process.
Deep wetting of porous electrodes
The long waiting time for filling the cells is due to the special characteristics of the electrode materials. Porous layers must be completely penetrated by the electrolyte to ensure optimum mass and charge transport. How long this takes depends on the chemical composition of the materials, the layer thickness and density, and the wetting properties of the electrolyte. So there are spots to intervene - ideally with the aid of methods that measure the wetting rate in advance rather than electrochemically in the cell.

Monitoring wettability with the Washburn method
Behind the name Washburn lies an elegant method for measuring the wetting speed. A precision force sensor detects the increase in mass over time caused by the rising of a liquid in a porous sample. Based on the resulting wetting rate K, different electrode materials can be compared with each other even before they are used in the cell. For example, this method could be used to determine the optimum proportion of carbon black in a slurry.

Electrode calendering and its influence on wettability
Results are also available on how electrode wettability is influenced by the parameters of the coating process (calendering) [1], which has a strong impact on the pore size. In principle, all conceivable factors influencing the wetting time can be investigated and thus optimized.
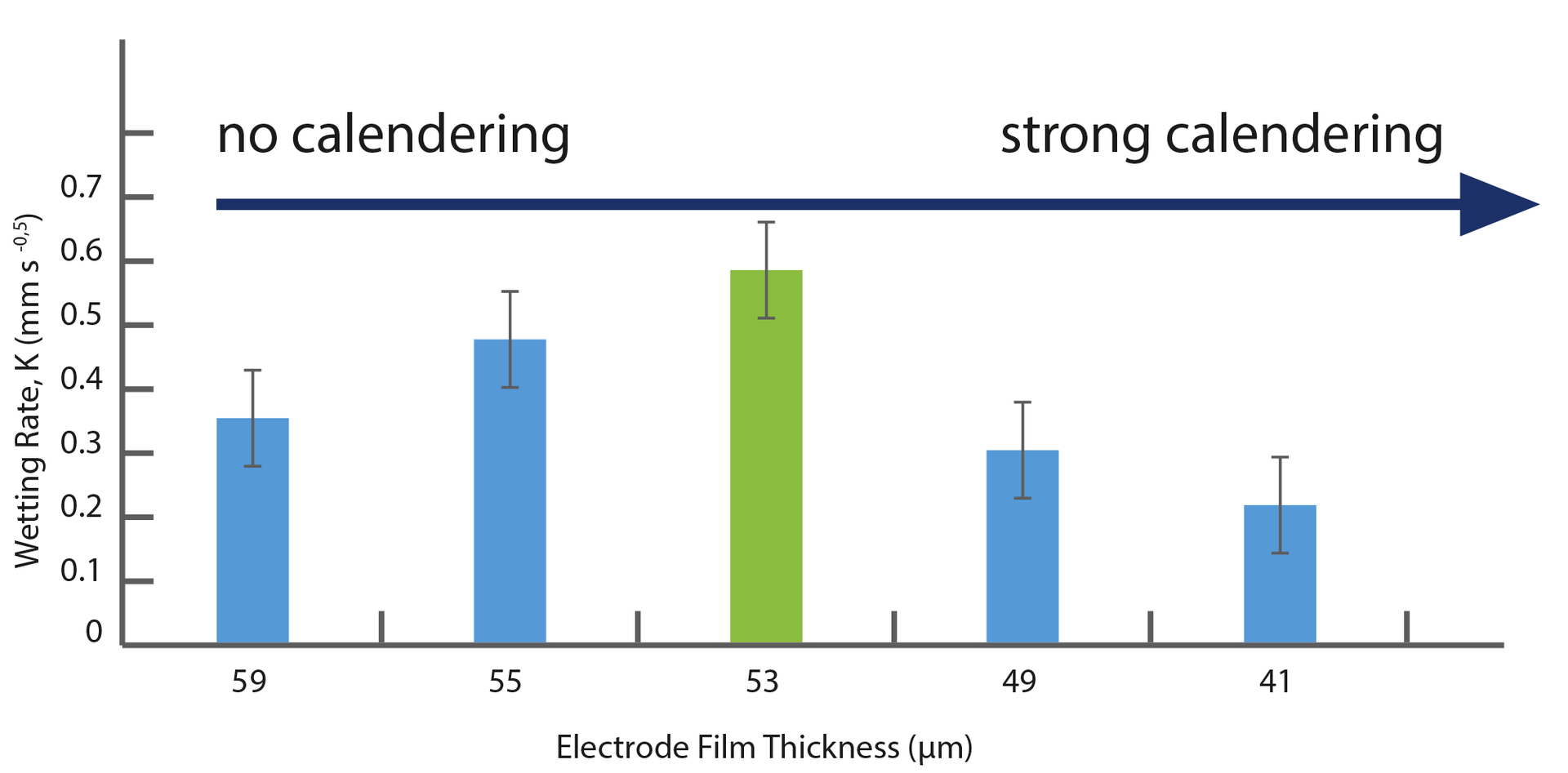
The role of the surface tension of the electrolyte
Wetting is always a process between two components and of course the properties of the electrolyte also influence the filling time. The lower the surface tension (SFT), the faster the wetting, which is why surface-active substances (surfactants) are frequently added to the electrolyte. Tensiometric measurements – which can be performed with the same instrument as the Washburn investigations – provide rapid results for the SFT and the effect of the additives.
Correlation between polarity and wetting
If we have just spoken of the direct correlation between SFT and wetting, this is only half the story. The interfacial chemical interactions that dominate wetting also depend on the polar properties of the electrolyte and the electrode material. With the aid of more in-depth investigations, these interactions can be recorded more precisely on the basis of the contact angle and the surface free energy (SFE) of the electrode material that is then accessible. The somewhat greater effort is worthwhile: Based on the SFE and its polar fraction, it is possible, for example, to calculate which properties of the electrolyte – or of the electrode material – would lead to the best possible wetting. Instead of carrying out investigations with trial-and-error methods, wetting can be optimized in a targeted manner based on meaningful result parameters.
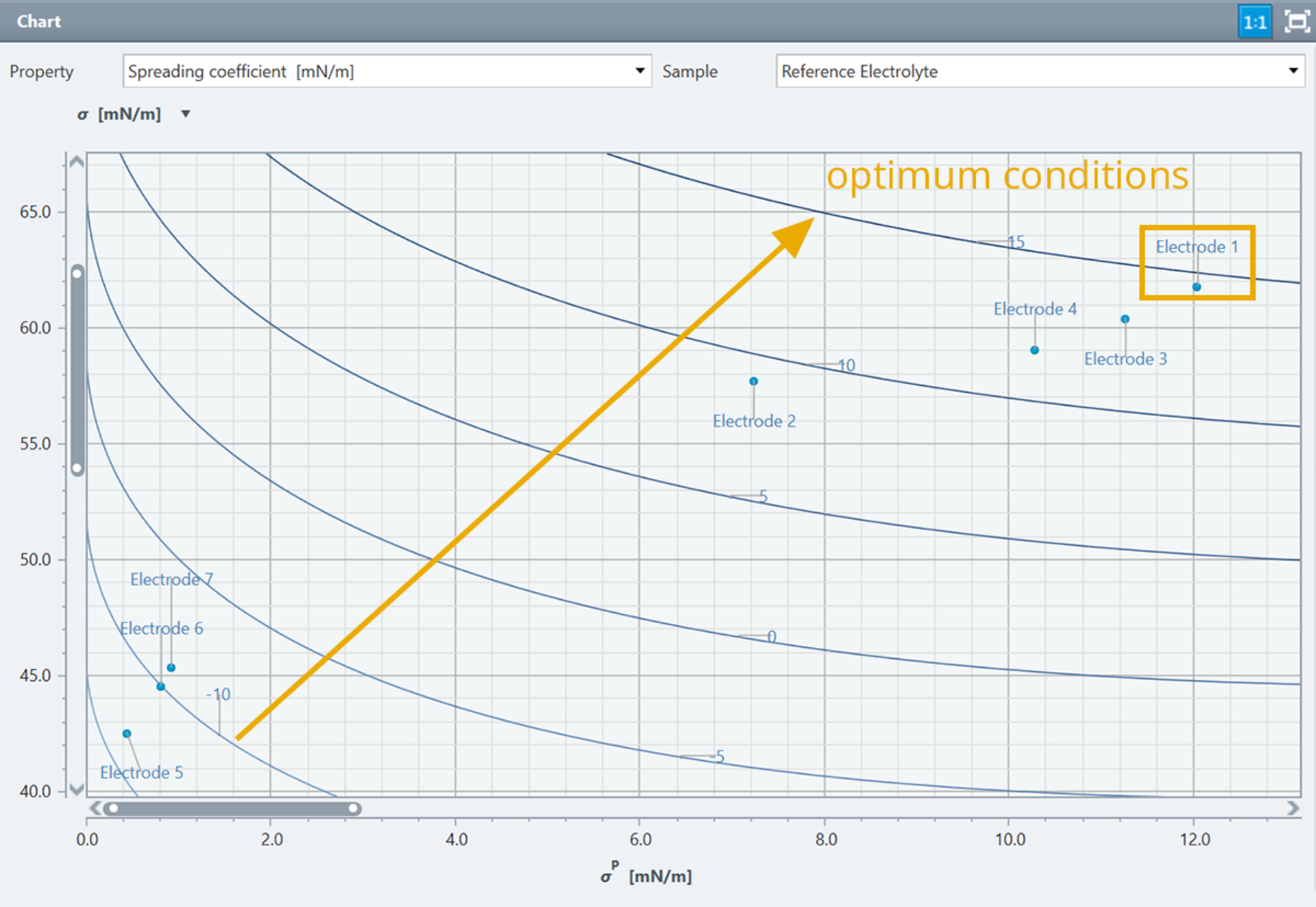
[1] Sheng, Yangping: Investigation of Electrolyte Wetting in Lithium Ion Batteries: Effects of Electrode Pore Structures and Solution. Theses and Dissertations 1080 (2015).